倉庫管理系統(tǒng) 畢業(yè)論文外文翻譯
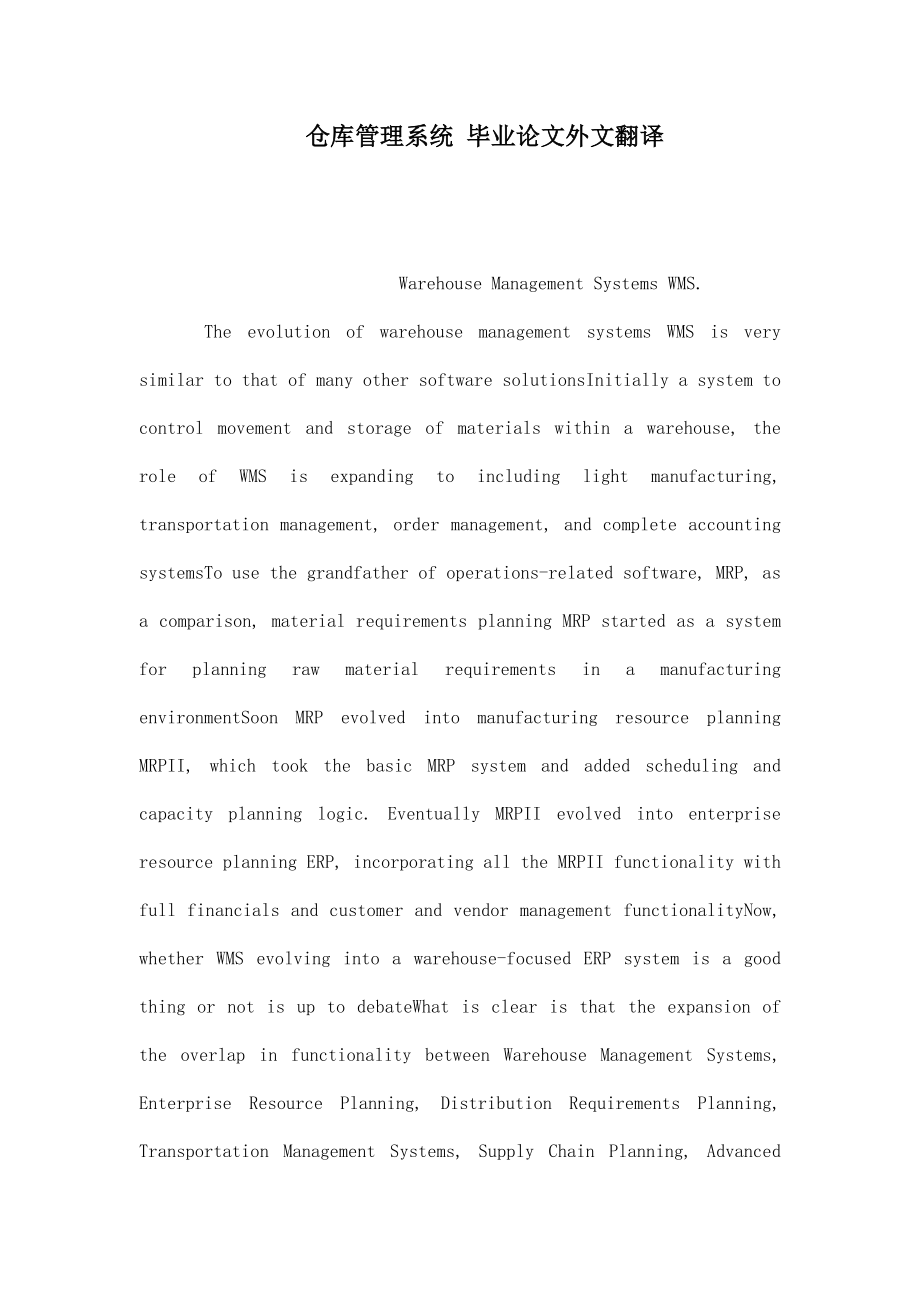


《倉庫管理系統(tǒng) 畢業(yè)論文外文翻譯》由會員分享,可在線閱讀,更多相關(guān)《倉庫管理系統(tǒng) 畢業(yè)論文外文翻譯(16頁珍藏版)》請在裝配圖網(wǎng)上搜索。
1、倉庫管理系統(tǒng) 畢業(yè)論文外文翻譯 Warehouse Management Systems WMS. The evolution of warehouse management systems WMS is very similar to that of many other software solutionsInitially a system to control movement and storage of materials within a warehouse, the role of WMS is expandin
2、g to including light manufacturing, transportation management, order management, and complete accounting systemsTo use the grandfather of operations-related software, MRP, as a comparison, material requirements planning MRP started as a system for planning raw material requirements in a manufacturin
3、g environmentSoon MRP evolved into manufacturing resource planning MRPII, which took the basic MRP system and added scheduling and capacity planning logic. Eventually MRPII evolved into enterprise resource planning ERP, incorporating all the MRPII functionality with full financials and customer and
4、vendor management functionalityNow, whether WMS evolving into a warehouse-focused ERP system is a good thing or not is up to debateWhat is clear is that the expansion of the overlap in functionality between Warehouse Management Systems, Enterprise Resource Planning, Distribution Requirements Plannin
5、g, Transportation Management Systems, Supply Chain Planning, Advanced Planning and Scheduling, and Manufacturing Execution Systems will only increase the level of confusion among companies looking for software solutions for their operations Even though WMS continues to gain added functionality, th
6、e initial core functionality of a WMS has not really changedThe primary purpose of a WMS is to control the movement and storage of materials within an operation and process the associated transactionsDirected picking, directed replenishment, and directed put away are the key to WMSThe detailed setup
7、 and processing within a WMS can vary significantly from one software vendor to another, however the basic logic will use a combination of item, location, quantity, unit of measure, and order information to determine where to stock, where to pick, and in what sequence to perform these operations A
8、t a bare minimum, a WMS should: Have a flexible location system. Utilize user-defined parameters to direct warehouse tasks and use live documents to execute these tasks. Have some built-in level of integration with data collection devices. Do You Really Need WMS? No
9、t every warehouse needs a WMSCertainly any warehouse could benefit from some of the functionality but is the benefit great enough to justify the initial and ongoing costs associated with WMSWarehouse Management Systems are big, complex, data intensive, applicationsThey tend to require a lot of initi
10、al setup, a lot of system resources to run, and a lot of ongoing data management to continue to runThat’s right, you need to "manage" your warehouse "management" systemOften times, large operations will end up creating a new IS department with the sole responsibility of managing the WMSThe Reality:
11、 The implementation of a WMS along with automated data collection will likely give you increases in accuracy, reduction in labor costs provided the labor required to maintain the system is less than the labor saved on the warehouse floor, and a greater ability to service the customer by reducing
12、 cycle timesExpectations of inventory reduction and increased storage capacity are less likelyWhile increased accuracy and efficiencies in the receiving process may reduce the level of safety stock required, the impact of this reduction will likely be negligible in comparison to overall inventory le
13、vels. The predominant factors that control inventory levels are lot sizing, lead times, and demand variabilityIt is unlikely that a WMS will have a significant impact on any of these factors. And while a WMS certainly provides the tools for more organized storage which may result in increased storag
14、e capacity, this improvement will be relative to just how sloppy your pre-WMS processes were Beyond labor efficiencies, the determining factors in deciding to implement a WMS tend to be more often associated with the need to do something to service your customers that your current system does not
15、support or does not support well such as first-in-first-out, cross-docking, automated pick replenishment, wave picking, lot tracking, yard management, automated data collection, automated material handling equipment, etc. Setup The setup requirements of WMS can be extensive. The characteristic
16、s of each item and location must be maintained either at the detail level or by grouping similar items and locations into categoriesAn example of item characteristics at the detail level would include exact dimensions and weight of each item in each unit of measure the item is stocked each, cases, p
17、allets, etc as well as information such as whether it can be mixed with other items in a location, whether it is rack able, stack height, quantity per location, hazard classifications, finished goods or raw material, fast versus slow mover, etcAlthough some operations will need to set up each item
18、 this way, most operations will benefit by creating groups of similar productsFor example, if you are a distributor of music CDs you would create groups for single CDs, and double CDs, maintaining the detailed dimension and weight information at the group level and only needing to attach the group c
19、ode to each itemYou would likely need to maintain detailed information on special items such as boxed sets or CDs in special packagingYou would also create groups for the different types of locations within your warehouse. An example would be to create three different groups P1, P2, P3 for the three
20、 different sized forward picking locations you use for your CD pickingYou then set up the quantity of single CDs that will fit in a P1, P2, and P3 location, quantity of double CDs that fit in a P1, P2, P3 location etcYou would likely also be setting up case quantities, and pallet quantities of each
21、CD group and quantities of cases and pallets per each reserve storage location group If this sounds simple, it is…well… sort of. In reality most operations have a much more diverse product mix and will require much more system setupAnd setting up the physical characteristics of the product and loc
22、ations is only part of the pictureYou have set up enough so that the system knows where a product can fit and how many will fit in that locationYou now need to set up the information needed to let the system decide exactly which location to pick from, replenish from/to, and put away to, and in what
23、sequence these events should occur remember WMS is all about “directed” movementYou do this by assigning specific logic to the various combinations of item/order/quantity/location information that will occur Below I have listed some of the logic used in determining actual locations and sequences
24、 Location SequenceThis is the simplest logic; you simply define a flow through your warehouse and assign a sequence number to each locationIn order picking this is used to sequence your picks to flow through the warehouse, in put away the logic would look for the first location in the sequence in
25、which the product would fit Zone LogicBy breaking down your storage locations into zones you can direct picking, put away, or replenishment to or from specific areas of your warehouseSince zone logic only designates an area, you will need to combine this with some other type of logic to determin
26、e exact location within the zone Fixed LocationLogic uses predetermined fixed locations per item in picking, put away, and replenishmentFixed locations are most often used as the primary picking location in piece pick and case-pick operations, however, they can also be used for secondary storage
27、 Random LocationSince computers cannot be truly random nor would you want them to be the term random location is a little misleadingRandom locations generally refer to areas where products are not stored in designated fixed locationsLike zone logic, you will need some additional logic to determine
28、 exact locations First-in-first-out FIFODirects picking from the oldest inventory first Last-in-first-out LIFOOpposite of FIFO. I didnt think there were any real applications for this logic until a visitor to my site sent an email describing their operation that distributes perishable goods dome
29、stically and overseas. They use LIFO for their overseas customers because of longer in-transit times and FIFO for their domestic customers Pick-to-clearLogic directs picking to the locations with the smallest quantities on handThis logic is great for space utilization Reserved LocationsThis is u
30、sed when you want to predetermine specific locations to put away to or pick fromAn application for reserved locations would be cross-docking, where you may specify certain quantities of an inbound shipment be moved to specific outbound staging locations or directly to an awaiting outbound trailer
31、imize CubeCube logic is found in most WMS systems however it is seldom usedCube logic basically uses unit dimensions to calculate cube cubic inches per unit and then compares this to the cube capacity of the location to determine how much will fitNow if the units are capable of being stacked into th
32、e location in a manner that fills every cubic inch of space in the location, cube logic will workSince this rarely happens in the real world, cube logic tends to be impractical ConsolidateLooks to see if there is already a location with the same product stored in it with available capacityMay also
33、 create additional moves to consolidate like product stored in multiple locations Lot SequenceUsed for picking or replenishment, this will use the lot number or lot date to determine locations to pick from or replenish from It’s very common to combine multiple logic methods to determine the best
34、 locationFor example you may chose to use pick-to-clear logic within first-in-first-out logic when there are multiple locations with the same receipt dateYou also may change the logic based upon current workloadDuring busy periods you may chose logic that optimizes productivity while during slower p
35、eriods you switch to logic that optimizes space utilizationOther Functionality/Considerations Wave Picking/Batch Picking/Zone PickingSupport for various picking methods varies from one system to anotherIn high-volume fulfillment operations, picking logic can be a critical factor in WMS selection
36、. See my article on Order Picking for more info on these methods Task InterleavingTask interleaving describes functionality that mixes dissimilar tasks such as picking and put away to obtain imum productivityUsed primarily in full-pallet-load operations, task interleaving will direct a lift truck
37、operator to put away a pallet on his/her way to the next pickIn large warehouses this can greatly reduce travel time, not only increasing productivity, but also reducing wear on the lift trucks and saving on energy costs by reducing lift truck fuel consumption. Task interleaving is also used with cy
38、cle counting programs to coordinate a cycle count with a picking or put away task Integration with Automated Material Handling Equipment If you are planning on using automated material handling equipment such as carousels, ASRS units, AGNS, pick-to-light systems, or separation systems, you’ll want
39、 to consider this during the software selection processSince these types of automation are very expensive and are usually a core component of your warehouse, you may find that the equipment will drive the selection of the WMSAs with automated data collection, you should be working closely with the e
40、quipment manufacturers during the software selection process Advanced Shipment Notifications ASNIf your vendors are capable of sending advanced shipment notifications preferably electronically and attaching compliance labels to the shipments you will want to make sure that the WMS can use this t
41、o automate your receiving process. In addition, if you have requirements to provide ASNs for customers, you will also want to verify this functionality Yard ManagementYard management describes the function of managing the contents inventory of trailers parked outside the warehouse, or the empty
42、 trailers themselvesYard management is generally associated with cross docking operations and may include the management of both inbound and outbound trailers Labor Tracking/Capacity PlanningSome WMS systems provide functionality related to labor reporting and capacity planningAnyone that has wo
43、rked in manufacturing should be familiar with this type of logicBasically, you set up standard labor hours and machine usually lift trucks hours per task and set the available labor and machine hours per shift. The WMS system will use this info to determine capacity and loadManufacturing has been us
44、ing capacity planning for decades with mixed resultsThe need to factor in efficiency and utilization to determine rated capacity is an example of the shortcomings of this processNot that I’m necessarily against capacity planning in warehousing, I just think most operations don’t really need it and c
45、an avoid the disappointment of trying to make it workI am, however, a big advocate of labor tracking for individual productivity measurementMost WMS maintain enough data to create productivity reportingSince productivity is measured differently from one operation to another you can assume you will h
46、ave to do some minor modifications here usually in the form of custom reporting Integration with existing accounting/ERP systemsUnless the WMS vendor has already created a specific interface with your accounting/ERP system such as those provided by an approved business partner you can expect to sp
47、end some significant programming dollars hereWhile we are all hoping that integration issues will be magically resolved someday by a standardized interface, we isn’t there yetIdeally you’ll want an integrator that has already integrated the WMS you chose with the business software you are usingSince
48、 this is not always possible you at least want an integrator that is very familiar with one of the systems WMS + everything else As I mentioned at the beginning of this article, a lot of other modules are being added to WMS packages. These would include full financials, light manufacturing, tran
49、sportation management, purchasing, and sales order managementI don’t see this as a unilateral move of WMS from an add-on module to a core system, but rather an optional approach that has applications in specific industries such as 3PLsUsing ERP systems as a point of reference, it is unlikely that th
50、is add-on functionality will match the functionality of best-of-breed applications available separatelyIf warehousing/distribution is your core business function and you don’t want to have to deal with the integration issues of incorporating separate financials, order processing, etc. you may find t
51、hese WMS based business systems are a good fit 倉庫管理系統(tǒng)( WMS ) 倉庫管理系統(tǒng)( WMS )的演變與許多其他軟件解決方案是非常相似的。最初的系統(tǒng)用來控制物料在倉庫內(nèi)的流動和貯存,倉庫的作用正在延伸到包括輕型制造業(yè),交通運輸管理,訂單管理,和完整的會計制度中。利用與先前的業(yè)務有關(guān)的軟件,制造資源計劃,作為一個比較,材料需求計劃( MRP )開始作為一個規(guī)劃要求,原材料的生產(chǎn)環(huán)境的系統(tǒng)。 物料需求計劃很快演變成以MRP系統(tǒng),補充調(diào)度和容量規(guī)劃為基礎(chǔ)的邏輯制造資源計劃( MRPII系統(tǒng))。最終MRPII系統(tǒng)演變成企業(yè)資源規(guī)劃( ER
52、P ),吸收所有的MRPII系統(tǒng)的功能包括充分的財務與客戶和供應商管理功能。現(xiàn)在,無論倉庫管理系統(tǒng)演變成一個以倉庫為中心的ERP系統(tǒng)是一件好事或不可達的辯論。清楚的是,在倉庫管理系統(tǒng),企業(yè)資源規(guī)劃,布局規(guī)劃要求,交通運輸管理系統(tǒng),供應鏈計劃,高級計劃與排程,以及制造執(zhí)行系統(tǒng)之間擴大重疊功能性只會增加那些尋找軟件解決方案業(yè)務的公司混亂水平。 盡管倉庫繼續(xù)獲得額外的功能,最初的倉庫管理系統(tǒng)的核心功能還沒有真正改變。其主要目的是控制管理系統(tǒng)在工藝操作相關(guān)聯(lián)的交易中的流動和材料儲存。定向采摘,定向補充,定向收集是倉庫的關(guān)鍵。從一個軟件供應商到另一個在一個管理系統(tǒng)中詳細的安裝和處理可以有一個很
53、大的差別,但是其基本邏輯將使用相結(jié)合的項目,地點,數(shù)量,度量單位,并以收集信息以確定在哪里儲存,在哪里挑選,以及以何種順序執(zhí)行這些操作。 一 最低限度,一個倉庫管理系統(tǒng)應采取下列措施 有一個靈活的定位系統(tǒng)。 利用用戶定義的參數(shù),指導倉庫任務和使用Live文件來執(zhí)行這些任務。 有一些內(nèi)置的一體化和數(shù)據(jù)收集設(shè)備結(jié)合體。 您是否真的需要倉庫管理系統(tǒng)? 并非每一個倉庫需要一個倉庫管理系統(tǒng)。當然,任何倉庫可受益于其中一些功能,但這些受益是否足以證明管理系統(tǒng)最初的和正在進行的相關(guān)費用是正確的?倉庫管理系統(tǒng)是大的,復雜的,數(shù)
54、據(jù)密集型的應用。他們往往需要大量的初始安裝,很多系統(tǒng)資源的運行,很多正在進行的數(shù)據(jù)管理為繼續(xù)運行。沒錯,你需要“管理”你的倉庫“管理”制度。一般情況下,大規(guī)模的行動最終將建立一個新的IS部門用來唯一負責管理倉庫管理系統(tǒng)。 二 現(xiàn)實 實施一個倉庫管理系統(tǒng)用來自動的數(shù)據(jù)收集將可能使你的準確性增加,減少勞動力成本(提供需要維持系統(tǒng)的勞動力少于物品保存在倉庫樓需要的勞動力)和更好地來服務客戶以降低周期。預期庫存減少和增加存儲容量的可能性較小。雖然在接收過程中增加了準確性和效率可能降低庫存安全水平,但這種降低產(chǎn)生的影響與整體庫存水平相比可以忽略不計??刂茙齑嫠脚孔钪饕囊蛩厥嵌喾N
55、尺寸,交貨時間和需求的變化,倉庫管理系統(tǒng)將對任何因素有重大影響是不可能。而且同時倉庫管理系統(tǒng)確實的為更多的有組織的存儲提供工具,因為這種存儲可能會導致更多的存儲容量,相對于這種改善您之前的倉庫管理系統(tǒng)是多么草率啊。除了勞動效率,決定實施倉庫管理系統(tǒng)的決定因素,往往與一些能滿足您的客戶的需求有更多關(guān)聯(lián),比如您目前的系統(tǒng)不支持(或不太支持)像先進先出,交叉對接,自動挑選補充,波采摘,多種跟蹤,停車場管理,自動數(shù)據(jù)采集,自動材料處理設(shè)備等 。 三 設(shè)置 倉庫管理系統(tǒng)的設(shè)置需求是廣泛的,每個項目和地點都必須保持在詳細或分組類似項目和地點分類。一個例子,項目詳細程度的特點將包括確切尺寸
56、和重量,每個項目在每個單位的項目儲備(項目,案件,托盤等),以及信息,如是否可以與其他物品混在一個位置,無論是的最高層次,最大堆疊高度,最高量的位置,危險性分類,半成品或原材料,快與慢動,等。盡管一些行動將需要用這種方式設(shè)立每個項目,但大多數(shù)業(yè)務將有利于創(chuàng)造群體的類似產(chǎn)品。例如,如果你是一個音樂CD分銷商,您將創(chuàng)建集團單一CD和雙張CD ,保持詳細的尺寸和重量的資料在組一級,只需要對每個項目附上組代碼。您可能會需要對特殊物品保持詳細的資料,如盒裝套或CD的特別包裝。您也可以為地域的不同類型在您的倉庫里創(chuàng)造群組。一個例子是,為您用于CD采摘的三種不同大小前瞻性采摘地點建立3個不同群體(小一,二,
57、三)。然后,您可以建立單一的光盤數(shù)量,將適合P1,P2和P3的位置,多種雙張CD適合在小一,二,小三的位置等。您可能還設(shè)立案件的數(shù)量,每個CD組光盤數(shù)量,貨箱的數(shù)量和光盤的每個后備存儲位置組。 如果這聽起來很簡單,但在現(xiàn)實中很多業(yè)務有更多元化的產(chǎn)品組合,將需要更多的系統(tǒng)設(shè)置。而且建立產(chǎn)品的物理特性和產(chǎn)品的位置只是藍圖的部分。你設(shè)定的使系統(tǒng)知道產(chǎn)品可以適合哪里并且多少產(chǎn)品將滿足這個地方已經(jīng)足夠了。您現(xiàn)在需要建立必要的信息,以讓系統(tǒng)決定從哪些位置選擇,補充,并采集,并在這些事件應該出現(xiàn)這些序列中(記得倉庫管理就是“指示”流動)。你分配具體邏輯的的做法使各種組合項目/訂單/數(shù)量/位置信息將出
58、現(xiàn)。 下面我列出一些用于確定實際位置和序列的邏輯 位置順序。這是最簡單的邏輯;您只需確定流經(jīng)你的倉庫和為每一個地點分配序列編號。 為了挑選這是把您選擇的在流經(jīng)的倉庫排序,在采集邏輯將尋求在第一位置的順序適合的產(chǎn)品。 區(qū)邏輯 。由于把你的儲存地點分到區(qū),您可以直接采摘,收集,或補充或特定地區(qū)的倉庫。自區(qū)邏輯唯一指定的一個地區(qū),則需要再加上一些其他類型的邏輯,以確定確切位置在禁區(qū)內(nèi)。 固定的位置。 邏輯使用預先確定的固定地點,每一項目中分揀,采集 ,和補充。固定地點是一塊采摘挑選和個案選擇的行動最常用的首要位置,但是,它們也可用于二級存儲。 隨機地點
59、。由于電腦不能真正隨機(也不想要他們)的任期隨機位置有點誤導。 隨機地點一般指的是產(chǎn)品不會儲存在指定的固定地點的地方。如Zone邏輯,您將需要一些額外的邏輯,以確定確切位置。 先入先出( FIFO的)。首先指示挑選最古老的庫存。 最后,先出( LIFO )。我不認為這種邏輯有任何實際應用,直到我的網(wǎng)站訪問者發(fā)送一封電子郵件,說明自己在國內(nèi)和海外銷售易腐貨物的行動。他們?yōu)楹M饪蛻羰褂肔IFO(因為長期在途中)和為國內(nèi)客戶使用FIFO。 挑選到清楚。用最少的人手挑選邏輯指示的地點。這種邏輯是巨大的空間利用率。 預留位置。這個是在預約具體地點采集時使用。從申請預留位置
60、將交叉對接,在那里你可以指定一定數(shù)量的入境貨物轉(zhuǎn)移到具體的舉辦地點外,或直接到等待出境拖車。 最大限度地立方。立方體邏輯中是在WMS系統(tǒng)發(fā)現(xiàn)最多的,盡管它很少使用。立方體邏輯基本上使用單位面積計算立方體(立方英寸每單位)。然后比較這個位置的立方體能力,以確定有多少適合?,F(xiàn)在,如果這些單位能堆疊成的位置,以填補每立方英寸的空間中的位置,立方體邏輯將工作。由于這很少發(fā)生在現(xiàn)實世界,立方體的邏輯往往是不切實際的。 很多序列。用于采摘或補充,這將使用大量批號或日期,以確定位置,以選擇或補充。這是非常常見的邏輯結(jié)合多種方法,以確定最佳的位置。例如您可以選擇使用挑選到清晰的邏輯內(nèi)先入先出邏輯當有多個地點以同樣的收據(jù)的日期。您也可能會根據(jù)目前的工作量改變的邏輯。在繁忙時段內(nèi)您可以選擇的邏輯,優(yōu)化生產(chǎn)力,同時在速度較慢時期您切換到邏輯,優(yōu)
- 溫馨提示:
1: 本站所有資源如無特殊說明,都需要本地電腦安裝OFFICE2007和PDF閱讀器。圖紙軟件為CAD,CAXA,PROE,UG,SolidWorks等.壓縮文件請下載最新的WinRAR軟件解壓。
2: 本站的文檔不包含任何第三方提供的附件圖紙等,如果需要附件,請聯(lián)系上傳者。文件的所有權(quán)益歸上傳用戶所有。
3.本站RAR壓縮包中若帶圖紙,網(wǎng)頁內(nèi)容里面會有圖紙預覽,若沒有圖紙預覽就沒有圖紙。
4. 未經(jīng)權(quán)益所有人同意不得將文件中的內(nèi)容挪作商業(yè)或盈利用途。
5. 裝配圖網(wǎng)僅提供信息存儲空間,僅對用戶上傳內(nèi)容的表現(xiàn)方式做保護處理,對用戶上傳分享的文檔內(nèi)容本身不做任何修改或編輯,并不能對任何下載內(nèi)容負責。
6. 下載文件中如有侵權(quán)或不適當內(nèi)容,請與我們聯(lián)系,我們立即糾正。
7. 本站不保證下載資源的準確性、安全性和完整性, 同時也不承擔用戶因使用這些下載資源對自己和他人造成任何形式的傷害或損失。
最新文檔
- 2025年防凍教育安全教育班會全文PPT
- 2025年寒假安全教育班會全文PPT
- 初中2025年冬季防溺水安全教育全文PPT
- 初中臘八節(jié)2024年專題PPT
- 主播直播培訓提升人氣的方法正確的直播方式如何留住游客
- XX地區(qū)機關(guān)工委2024年度年終黨建工作總結(jié)述職匯報
- 心肺復蘇培訓(心臟驟停的臨床表現(xiàn)與診斷)
- 我的大學生活介紹
- XX單位2024年終專題組織生活會理論學習理論學習強黨性凝心聚力建新功
- 2024年XX單位個人述職述廉報告
- 一文解讀2025中央經(jīng)濟工作會議精神(使社會信心有效提振經(jīng)濟明顯回升)
- 2025職業(yè)生涯規(guī)劃報告自我評估職業(yè)探索目標設(shè)定發(fā)展策略
- 2024年度XX縣縣委書記個人述職報告及2025年工作計劃
- 寒假計劃中學生寒假計劃安排表(規(guī)劃好寒假的每個階段)
- 中央經(jīng)濟工作會議九大看點學思想強黨性重實踐建新功