機械設計及自動化畢業(yè)論文設計摩擦片表面去毛刺機床設計
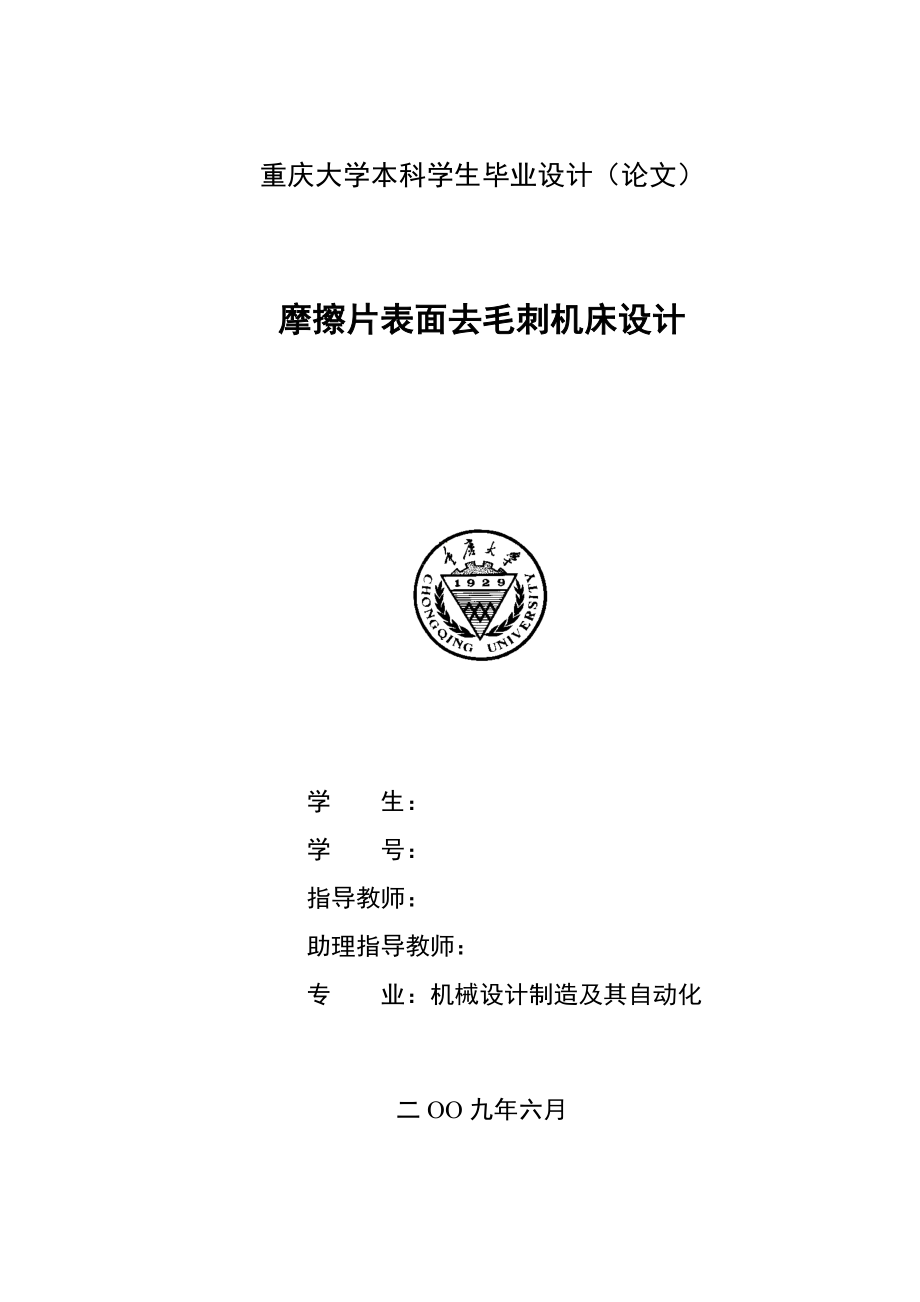


《機械設計及自動化畢業(yè)論文設計摩擦片表面去毛刺機床設計》由會員分享,可在線閱讀,更多相關《機械設計及自動化畢業(yè)論文設計摩擦片表面去毛刺機床設計(37頁珍藏版)》請在裝配圖網(wǎng)上搜索。
1、重慶大學本科學生畢業(yè)設計(論文) 摩擦片表面去毛刺機床設計 學 生: 學 號: 指導教師: 助理指導教師: 專 業(yè):機械設計制造及其自動化 二OO九年六月 摘 要 本文針對摩擦片表面去毛刺的加工現(xiàn)狀,著重對砂帶磨削機床進行了相關研究與設計。根據(jù)設計任務的要求,運用專用機床設計方法,通過各種計算校核,運用制圖表達等,最終實現(xiàn)機床的這一功能,可以很好的完成摩擦片表面去毛刺這一加工任務。本文的主要內(nèi)容包括: 1.介紹目前摩擦片表面去毛刺的加工現(xiàn)狀和國內(nèi)外砂帶磨床的發(fā)展現(xiàn)狀和發(fā)展趨勢,以及砂帶磨床
2、設計的簡介。 2.砂帶磨床總體方案的確定,主要是確定機床的總體布局,各功能模塊的實現(xiàn)方案,以及主要技術參數(shù)的選擇與確定和傳動鏈的計算。 3.砂帶磨床的各功能模塊的詳細設計,主要是主軸,磨頭,工作臺,進給系統(tǒng)的詳細設計,包括各部分的結構,裝配以及功能分析。 關鍵詞:摩擦片,去毛刺,砂帶磨削,機床 ABSTRACT In this paper, the friction surface of the processing status of deburring, abrasive belt grindin
3、g machine tool focused on a related research and design. According to the design of tasks, the use of Special Purpose Machine design methodology, verification through a variety of computing, such as the use of cartographic expression, and ultimately the function of machine tools can be a very good s
4、urface friction of the completion of the processing task of deburring. The main contents of this article include: 1. Introduced friction surface to the current processing status of burr abrasive belt grinding machine at home and abroad of the status quo and development trend of development, as wel
5、l as a brief introduction of abrasive belt grinding machine design. 2. Abrasive belt grinding machine to determine the overall program, the main tool is to determine the overall layout of the realization of the function modules, as well as the choice of main technical parameters and the identificat
6、ion and calculation of transmission chain. 3. Abrasive belt grinder features of the detailed design of modules, mainly spindle, grinding head, table, into the detailed design of the system, including the part of the structure, assembly and functional analysis. Key words:Friction plate, Deburri
7、ng, Belt grinding, Machine Tool 目 錄 中文摘要.....................................................................................................Ⅰ ABSTRACT................................................................................................Ⅱ 1緒論..........
8、..................................................................................................1 1.1 摩擦片去毛刺的加工現(xiàn)狀.............................................................................1 1.2 砂帶磨床介紹..........................................................................................
9、..1 1.2.1砂帶磨床發(fā)展背景介紹............................................................................1 1.2.2 砂帶磨床的發(fā)展現(xiàn)狀與趨勢.....................................................................1 1.2.3砂帶磨床的設計介紹...............................................................................4 2總體方案設計
10、............................................................................................7 2.1工件加工工藝分析.......................................................................................7 2.2機床總體布局...........................................................................................
11、..7 2.3機床主要技術參數(shù)的確定..............................................................................8 3磨頭設計....................................................................................................9 3.1磨削分析與計算以及磨頭結構設計..................................................................9
12、 3.1.1磨削力的理論計算..................................................................................9 3.1.2磨削功率計算........................................................................................9 3.1.3砂帶張緊力計算...............................................................................
13、....10 3.1.4磨頭結構的尺寸設計.............................................................................10 3.1.5砂帶尺寸選擇與計算.............................................................................11 3.1.6砂帶磨削過程中的受力分析....................................................................11
14、 3.1.7張緊機構及快換操縱機構和調(diào)偏機構........................................................12 3.2主軸設計.................................................................................................12 3.3帶輪設計.................................................................................................
15、18 4工作臺設計..............................................................................................21 4.1渦輪蝸桿傳動設計.....................................................................................21 4.2絲桿螺母傳動設計.............................................................................
16、........22 5進給系統(tǒng)設計..........................................................................................24 5.1經(jīng)給系統(tǒng)驅(qū)動電機選擇...............................................................................24 5.2傳送帶設計...............................................................................
17、...............25 6機床功能分析..........................................................................................26 6.1磨頭功能分析...........................................................................................26 6.2磁性工作臺功能分析............................................................
18、......................26 6.3進給系統(tǒng)功能分析.....................................................................................27 7結論..........................................................................................................29 致謝...........................................................
19、..................................................30 參考文獻.....................................................................................................31 1 緒論 1.1 摩擦片去毛刺加工現(xiàn)狀 本課題中,研究解決摩擦片表面去毛刺的解決方法。由于摩擦片屬于薄板平面零件,在其經(jīng)過一系列加工過程后,表面總會產(chǎn)生一些飛邊毛刺。為了到達其使用要求,必須將表面毛刺去除,以達到其工藝標準。目前工業(yè)生產(chǎn)中,薄板
20、平面零件除毛刺工藝雖然有很多種,但大多采用機械去毛刺方法,去毛刺動作過程及原理、適用范圍各不相同??偟膩碚f有以下幾種[1]:手工去毛刺工藝;滾筒去毛刺工藝;震動光飾去毛刺;磨削去毛刺;噴射去毛刺等。由于在薄板平面零件生產(chǎn)中,有些零件必須去毛刺后才可以轉入后續(xù)加工或進入產(chǎn)品裝配,交付用戶使用。從經(jīng)濟合理的角度考慮,不同的此類零件,應選用各種不同的去毛刺工藝,以確保產(chǎn)品質(zhì)量好、生產(chǎn)效率高、成本低[2]。 本課題從這些方面考慮,將選用磨削去毛刺工藝來解決本課題問題。在磨削去毛刺工藝中,采用電動砂輪機和砂布帶輪手工修理雖然工時費用低,但工人操作安全性較差,工作效率不高。而砂帶磨削擁有一次磨削寬度大、
21、磨削效率高、系統(tǒng)振動小且穩(wěn)定性好等特點。由于摩擦片屬于加工易變形的厚度不大的平板類零件,且批量生產(chǎn)、數(shù)量較多,因而選用砂帶磨削設備能很好的解決本課題問題,即設計摩擦片表面去毛刺砂帶磨削機床。 1.2 砂帶磨床介紹 1.2.1 砂帶磨床發(fā)展背景介紹 砂帶磨床是一種既古老而又新興的工藝。近30多年來, 粘滿尖銳砂粒的砂布或砂紙制成一種高速的多刀多刃連續(xù)切削工具用于砂帶磨床之后, 砂帶磨削技術獲得了很大的發(fā)展。這種砂帶磨削技術遠遠超越了原有的只用來加工和拋光的陳舊概念?,F(xiàn)在砂帶磨床的加工效率甚至超過了車、銑、刨等常規(guī)加工工藝,加工精度已接近或達到同類型機床的水平,機床功率的利用率領先于所有
22、的金屬切削機床,應用范圍不僅遍及各行各業(yè),而且對幾乎所有的材料,無論是金屬還是非金屬都可以進行加工[3]。長期以來不大引人注意的砂帶磨削工藝現(xiàn)在正進入現(xiàn)代化發(fā)展的新階段。 1.2.2砂帶磨床的發(fā)展現(xiàn)狀與趨勢[3] 砂帶磨削在世界各國、特別是美國和西德的應用非常廣泛,從日用的湯匙到宇航器具的蜂窩夾層結構各行各業(yè)無不競相采用。 ① 美國 美國是在世界上最早研制砂帶磨床的國家。第一臺砂帶磨床用于加工木材,隨后廣泛用于加工金屬。據(jù)美國對全國金屬加工設備調(diào)查表明,70 年代,美國的砂帶磨床已突破4 萬臺。到90 年代,每10 臺磨床至少有一臺砂帶磨床,而拋光機床中每3 臺就有 1 臺是砂帶拋光機
23、。在美國注冊砂帶磨床的公司和工廠多達53 家,著名的工廠有哈蒙德公司、希爾艾克米公司、泰姆塞費斯公司等,它們主要生產(chǎn)運輸帶式平面砂帶磨床、無心外圓砂帶磨床、大平面寬砂帶磨床。在美國,砂帶磨床的應用遍及所有行業(yè)。隨著砂帶制造工藝的不斷改善,機床結構剛性的加強,機床功率的增加,自動化程度的提高,使機床金屬切削率逐年增加,加工精度有了大幅度的提高,同時加工范圍和對象也不斷擴大。 ② 西德 西德從50 年代就開始研究砂帶磨削,各型砂帶磨床都有生產(chǎn),瓦德里??票S(W aldrich2 cobnrg) 和文得令登(vander linden) 廠都是生產(chǎn)大型機床的著名工廠。他們利用長期生產(chǎn)大型機床的
24、經(jīng)驗,利用導軌磨床的部件,如靜壓導軌道、龍門結構、大型真空吸附高精度工作臺等,設計和制造了大量的寬砂帶平面磨床。 ③ 日本 日本自行生產(chǎn)砂帶磨床的工廠主要有松下電機廠、東芝機械廠等,已生產(chǎn)各類型平面砂帶磨床、無心外圓砂帶磨床。80 年代,東芝機械廠制成了55L -V K 型超小氣動砂帶機,突破以前無法用砂帶加工小溝槽的這一難題,值得注意。 ④ 國內(nèi) 國內(nèi)的砂帶磨削技術是在20世紀70年代末才得以真正發(fā)展,隨著國內(nèi)的改革開放,砂帶磨削技術日益引起了各行業(yè),研究單位和企業(yè)的重視,加之砂帶制造技術的提高及品種的增加,使得砂帶磨削設備的研究和生產(chǎn)也得到了較大的發(fā)展。目前國內(nèi)的砂帶制造廠家有鄭州
25、白鴿等數(shù)十家企業(yè)等,砂帶磨削設備的生產(chǎn)廠家有重慶三磨海達磨床公司等十來家企業(yè),研究單位有鄭州三磨所,華僑大學,廣東工業(yè)大學,湖南大學,東北大學,重慶大學等多家科研院所和高校。 1).砂帶磨床的應用 A .應用范圍: a.大型平面的厚板、中等厚板、薄板、特別是耐熱難加工材料,如不銹鋼板、鈦合金板等。 b 大量生產(chǎn)的平面零件。如電子工業(yè)的印刷板、變壓器硅鋼片、齒輪箱體等。 c 型面加工。各種大小尺寸的復雜型面,特別是發(fā)動機葉片。如采用直徑小于 25mm 的砂輪進行加工,砂輪會很快磨損,而且也無法確保精度,而砂帶磨床則能以穩(wěn)定的速度工作,精度、粗糙度精度、效率都很高。 d 用砂輪磨床加工
26、大型容器、大尺寸棒料、管料時砂輪直徑要大于125mm ,如改用砂帶磨床,效率至少可提高一倍。 e 對于直徑大于 25mm 的長內(nèi)孔進行磨削、拋光,尤其是薄壁內(nèi)孔最為適用。 B 砂帶磨削的加工精度 砂帶磨床的一般精度最高可以保證在01005mm ,美國森斯特蘭(Sundstrand) 廠的“H i-Grind”砂帶平面磨床加工直徑為380mm 的汽車發(fā)動機鑄鐵缸蓋,不平度已達到0.001mm。 C 砂帶磨床的生產(chǎn)效率 在加工效率方面,砂帶磨床遠高于砂輪磨床,一般約為 4 倍。美國的“H i- Grind”砂帶平面磨床,每分鐘切除每立方英寸的金屬切屑所需功率僅為立式平面磨床的1/ 3。砂
27、帶磨床用于切除金屬的功率可高達其輸入功率的96% , 幾乎全部轉換為有用功。 D 加工成本: 砂帶磨床高速發(fā)展的原因之一是經(jīng)濟效果十分顯著。日本曾就砂帶磨削的生產(chǎn)成本進行了詳細的分析,認為砂輪磨床的成本比砂帶磨床高,砂帶磨床要比銑床的生產(chǎn)成本低。例如,以切除鑄鐵工件每一立方英寸切屑計,用砂帶磨床比用砂輪磨床成本低 25%。 2) 砂帶磨床的發(fā)展趨勢[4] A 繼續(xù)提高生產(chǎn)效率 a 提高磨削速度和增大機床功率。長期以來,砂帶磨床的砂帶工作速度一直停留在 20m/s~ 30m/s。據(jù)美國制造工程學會研究報告說, 100m/s 的高速砂帶磨床已在試驗。在過去較長一個時期,機床功率從每一平方
28、英寸砂帶面積 4.4kW~ 7.5kW ,到了 70 年代已提高到 18.5kW~ 26kW ,機床功率現(xiàn)如今為200kW以上的已屢見不鮮,為提高金屬切除率,機床的功率必將增大。 b 發(fā)展寬砂帶磨削,擴大寬砂帶磨床的使用范圍。目前,最大寬度的砂帶磨床可磨削 4.9m 寬的平面。據(jù)報導,宇航器具、大型艦艇、高能物理的研究和應用都要大量使用高精度、高粗糙度精度的板材。提高板材加工效率的途徑就是要發(fā)展寬砂帶磨床。 B 提高加工精度 西德瓦德里??票S在砂帶磨床上大量采用高精度常規(guī)磨床的結構。美國森斯特蘭廠的砂帶磨床,按照砂帶磨削工作的特性,設計相應的專用部件以便提高機床的加工精度。但就砂帶磨床
29、本身來說,砂帶制造精度的提高,同樣是很重要的。 C 延長砂帶壽命 延長砂帶壽命是降低砂帶磨床加工成本最為關鍵的一個因素。目前,使用壽命已從 2h~ 4h 提高到 8h~12h 。為進一步延長砂帶壽命,除改善磨料、粘結劑基底之外,國外還從砂帶磨損的機理上解決延長壽命的問題。砂帶磨損主要“粘蓋”和“磨鈍”,特別是“粘蓋”現(xiàn)象最為嚴重,一旦出現(xiàn)“粘蓋”,砂帶就無法繼續(xù)使用。因此,美國最近在制造砂帶中已加添抗“粘蓋”的化學添加劑。 D 提高自動化程度 多頭砂帶磨床、運輸帶式或回轉臺式砂帶磨床都是實現(xiàn)自動化的一些手段。至于數(shù)控砂帶磨床,早在 1973 年在西德就開始使用,西德的 FBSA – 8
30、00 、 FBSA - 1000mm 大平面砂帶磨床也早已開始應用。 E 擴大萬能性和適應性 一機多能、一機多頭機床,上下表面同時加工的機床,磨完工件上表面后工件自行翻身再磨下表面的機床,連續(xù)加工而工件自動退回的機床,機電一體化的各種砂帶磨床,隨著工業(yè)發(fā)展已相繼問世和投入使用。砂帶磨床的萬能性、適應性今后還會進一步發(fā)展,使砂帶磨床在工業(yè)生產(chǎn)中無所不能。 1.2.3 砂帶磨床的設計介紹 砂帶磨削是根據(jù)工件形狀,用相應的接觸方式及高速運動的砂帶對工件表面進行磨削和拋光的一種新工藝。隨著汽車、建材、裝飾工業(yè)、模具工業(yè)及其它輕工業(yè)的進步和發(fā)展,對金屬和非金屬材料特別是難加工材料如塑料、皮革、橡
31、膠、不銹鋼、陶瓷等表面機械加工質(zhì)量、生產(chǎn)率及勞動環(huán)境提出了越來越高的要求,用一般傳統(tǒng)的切削加工方法已難以滿足這些要求。在過去的五、六十年內(nèi),砂帶磨削作為一種新工藝,在這些加工領域發(fā)揮著越來越大的作用。砂帶磨床主要用來作為粗磨、去毛刺、大余量磨削、精磨、細磨、裝飾拋光、無心磨以及成形磨削之用。在現(xiàn)代工業(yè)中,砂帶磨削技術以其獨具的加工特點被視為是一種很重要的加工方法。國外有專家曾把砂帶磨床比作“未來的巨人”來加以評述[5]。 1) 砂帶磨削原理: 實現(xiàn)砂帶磨削加工的主要方法有:砂帶自由張緊法、帶有接觸輪的轉動砂帶法和接觸板法。最常用的是帶有接觸輪的轉動砂帶法。如圖 1 所示: 砂帶套在傳動輪
32、、接觸輪的外表面上,并使砂帶張緊和高速運動,根據(jù)工件形狀和加工要求,以相應接觸方式和適當磨削參數(shù)對工件進行磨削或拋光。 砂帶磨削的基本部件有: A 主軸傳動裝置。有單速或具有較大靈活性的變速傳動,有時裝有可逆電動機,以改變砂帶的運動方向。皮帶速度為 10~ 50m/ min , 通常取16 ~ 30m/min ,主傳動裝置的功率,在每10mm 寬的砂帶上是0.3~0. 7kW。 圖 1 :接觸輪式砂帶磨削 B 砂帶張緊裝置。保持磨削及導向時砂帶的適當張力在砂帶磨削過程中起到重要作用,它影響到砂帶的切削性能和加工零件表面粗糙度。當增加砂帶拉力時,可提高金屬切除量,但同時也提高表面
33、粗糙度值和磨料覆蓋層的消耗量。經(jīng)試驗表明,砂帶的張力在6~8N/ mm 范圍內(nèi),在逆磨削時每次行程能切出最大的金屬量。拉緊機構有各種形式,從簡單的機械或彈簧方法到寬砂帶與重負載磨削機床用的氣動及液壓拉緊裝置。同時,為了獲得最大的生產(chǎn)率,必須使更換砂帶的時間最少,通常操作者能在1min 之內(nèi)更換砂帶。 C 砂帶導向裝置。砂帶工作時, 惰輪或張緊輪應當可以調(diào)整,使砂帶定位及對中,根據(jù)砂帶的寬度,這一裝置可以手動或自動。砂帶寬度大于 200mm 時,通常使用自動導向裝置,使接觸輪與張緊輪之間的砂帶自動對正。 D 接觸輪。接觸輪在磨削點上支承砂帶,其本體是用鋁或鋼制成,輪上覆蓋橡膠、纖維、毛氈或其
34、它材料制造的彈性圈(厚度為3~15mm)。根據(jù)需要,可制成各種密度橡膠輪,輪的表面制成交錯開槽式或平滑式。使用各種橡膠化合物作為接觸輪的覆蓋面,以滿足一定的磨削要求。這些化合物包括:氯丁橡膠、乙烯樹脂、硅酮橡膠、氯硫酸化聚乙烯合成橡膠。 E 若在砂帶后面安裝一塊型板(鋼、硬質(zhì)合金或鑄鐵平板)來代替接觸輪,則可完成磨邊、四邊形、端面、平面及精磨工作,保證零件的平面度或直線性。 此外還有吸塵系統(tǒng)等。 2) 砂帶磨削特點 砂帶與易損壞的工具如用于單刃車削、銑削、砂輪磨削等工具相比,具有下列特點: A 加工效率高。經(jīng)過精選的針狀砂粒采用先進的“靜電植砂法”,使砂粒均勻直立于基底、且鋒口向上、
35、定向整齊排列,等高性好,容屑間隙大,接觸面小,具有較好的切削性能。應用這一多刀多刃的切削工具進行磨削加工,對鋼材的切除率已達每 mm 寬砂帶 200~600 mm3 / min。 B 加工表面質(zhì)量高。砂帶磨削時接觸面小摩擦發(fā)熱少,且磨粒散熱時間間隔長,可以有效地減少工件變形及燒傷,故加工精度高,尺寸精度可達0.002mm,平面度可達0. 001mm。另外,砂帶在磨削時是柔性接觸,具有較好地磨削、研磨和拋光等多重作用,再加上磨削系統(tǒng)振動小,磨削速度穩(wěn)定使得表面加工質(zhì)量粗糙度值小,殘余應力狀態(tài)好,工件的粗糙度可達 Ra0. 4~0. 1μm ,且表面有均勻的粗糙度。但由于砂帶不能修整,故砂帶磨削
36、加工精度比砂輪磨削略低。 C 工藝靈活性大,適應性強。砂帶磨削可以方便地用于平面、外圓、內(nèi)圓磨削、復雜的異形面加工、切削余量 20mm 以下的粗加工磨削、去毛刺和為鍍層零件的預加工、拋光表面、消除板坯表面缺陷、刃磨和研磨切削工具、消除焊接處的凸瘤、代替鉗工作業(yè)的手工勞動。除了有各種通用、專用設備外,設計一個砂帶磨頭能方便地裝于車床、刨床和銑床等常規(guī)現(xiàn)成設備上,不僅能使這些機床功能大為擴展,而且能解決一些難加工零件如超長、超大型軸類、平面零件、不規(guī)則表面等的精密加工。 D 砂帶有很大的彈性, 因而整個系統(tǒng)有較高的抗振性。 E 砂帶尺寸可很大,適用于大面積高效率加工,且設備簡單,操作安全,使
37、用維護方便,更換砂帶和培訓機床操作人員花費時間較少。 F 在加工過程中砂帶增長,外形和尺寸達不到高精度,加工零件上的尖銳突出部位和用細粒度磨料精磨困難,砂帶的堅固性比較低,同時在大多數(shù)情況下砂帶不可能修正,所以使用期限短。 3) 砂帶磨床設計: 砂帶磨床設計一般包括下面三部分內(nèi)容: A 傳動設計:一般來說,機床傳動設計相對較簡單,主要由三方面組成: a 砂帶的主運動 b 砂帶的進給運動 c 工件的進給運動。 B 主要機構設計: a 砂帶張緊裝置 b 接觸輪設計。 C 主要技術參數(shù)選擇:砂帶速度、砂帶長度、寬度、砂帶電動機功率。 2 總體方案設計 2.1
38、 工件加工工藝分析 本課題中,研究摩擦片表面去毛刺的解決方法,上一章節(jié)中對其加工現(xiàn)狀做了簡要介紹,可以看出,現(xiàn)有的加工方法中砂帶磨削應該是一種經(jīng)濟實惠的方法。根據(jù)《中華人民共和國機械行業(yè)標準——工程機械制動摩擦片技術條件》(JB/T 8817-1998),摩擦片加工過后,其外觀質(zhì)量要求為:摩擦片的外觀不應有影響使用的龜裂、傷痕、分層、氣泡、翹曲、扭曲等缺陷。同時,摩擦片的推薦材質(zhì)一般有銅絲石棉編織帶、鋼纖維樹脂模壓型、石棉橡膠樹脂模壓型,本課題中將重點針對鋼纖維樹脂模壓型這一類進行專用砂帶磨床設計。由于摩擦片屬于薄板工件,往往其厚度在幾到幾十毫米之間,因而在加工過程中難于對其定位夾緊,且易變
39、形,所以在加工過程中必須特別注意。摩擦片的表面去毛刺這一加工過程,可以理解為對其表面進行精加工,或者可以看成對其表面進行拋磨,以最終達到使用要求,所以在加工過程中沒有大的磨削量。最終摩擦片加工后將達到:尺寸精度 0.005mm ,平面度 0.001mm ,工件粗糙度 Ra 0.4-0.1 um 。針對以上問題,下面將詳細敘述其解決辦法。 首先,摩擦片表面去毛刺只是對表面進行加工,因而所要設計的砂帶磨床將定義為平面砂帶磨削磨床。就平面砂帶磨削而言,實現(xiàn)平面磨削的方式只能是接觸輪式和壓磨板式,因此平面砂帶磨削的接觸方式、工件運動軌跡以及磨頭結構的布局和組合形式等都是以此為基礎的[6]。本設計將采
40、用接觸輪式設計。 其次,針對摩擦片屬于薄板工件,難于定位夾緊、易變形等特點,且只對鋼纖維樹脂模壓型這一類進行磨床設計。將采用磁臺對其加緊定位,傳輸帶進行工件進給的組合方式來實現(xiàn)。 最后,由于加工過程中,不需要大的磨削量,所以磨頭將設計為固定,即磨削主運動為固定,磨削量的控制將由一個微變升降工作臺來實現(xiàn)。 2.2 機床總體布局 上文已經(jīng)提到,將設計一個平面砂帶磨削機床,且主要需要一個磨頭、磁臺、傳輸帶、工作臺組合成一臺機床。因而,將采用傳輸帶式平面砂帶磨床的形式,簡明布局見圖2: 由圖分析,工件隨傳輸帶一次進入磨削區(qū)域,由磁臺對其定位夾緊,效率高,易于實現(xiàn),操作很簡單,便于自動化。
41、 1-磨頭 2-工件 3-磁臺 4-工作臺 5-傳輸帶 圖 2 :機床總體布局示意圖 2.3 機床主要技術參數(shù)的確定 砂帶磨床的主要技術參數(shù)設計包括磨削速度即砂帶速度;砂帶長度、寬度;工件進給速度即傳送帶速度;驅(qū)動砂帶電機功率。 由于去毛刺屬于輕載精加工,一般砂帶速度選擇為 25-35 m/s ,本設計中將選用 30 m/s ,即 Vs=30 m/s 。此外工件速度將定于 3 m/min,即 Vw=3 m/min ,以此保證工件加工的足夠精度。 砂帶磨床主要參數(shù)選擇如下: 砂帶速度:Vs=30 m/s 工件進給速度:Vw= 3m/min 砂帶:1950mm
42、 200 mm(長度寬度)( VSM KK711 422) 砂帶磨頭電機額定功率:15 Kw ( Y160L-4) 加工范圍:工件直徑200mm,厚度 3-20 mm 傳送帶尺寸:1800 mm220 mm(長度寬度) 磁臺尺寸:200mm200mm(長度寬度) 進給系統(tǒng)電機額定功率:2.2 Kw (Y132S-8) 電源:380V/220V 50HZ 磨削方式:干磨 3 磨頭設計 3.1 磨削分析與計算以及磨頭結構設計 3.1.1 磨削力的理論計算: 磨削力是研究砂帶磨削過程中的一個極為重要的參數(shù),它和砂帶的磨損,磨削表面質(zhì)量及比磨削能等有著直
43、接關系。而且磨削力易于測量和控制,因此可以用磨削力診斷磨削狀態(tài),作為適應控制的評定參數(shù)[7]。且通過磨削力的計算可以對磨床的后續(xù)設計做好準備。一般來說,磨削力可以分解為法向和切向兩個方向的力,具體計算如下: 已知:砂帶速度 Vs=30m/s,工件速度Vw=3m/min,砂帶寬度 B=200mm,有效磨削深度 ap=0.01mm,比磨削能 Us=800kg/mmmm。 根據(jù)公式計算如下: 法向磨削力:Fn=(UsB)/Vs (3-1) =511N 切向磨削力:Ft=(UsB)/
44、 (3-2) =355N 由于砂帶磨削其磨削分力的比例(即切向力和法向力之比)不同與常規(guī)的車、刨、銑等[8]。一般的車、銑等工序的切向分力是法向風力的 2 - 3 倍;而砂帶磨削的情況卻正好相反,因為起磨削深度和進給量均很小,而磨粒的切削刃鈍圓半徑較大且為負前角切削的緣故,經(jīng)實驗研究表明,砂帶磨削時一般為: Ft/Fn=0.33-0.7 (3-3) 本設計中,F(xiàn)t/Fn =355N/511N=0.69,所以滿足這一規(guī)律,即說明各參數(shù)設定合適。 3.1
45、.2 磨削功率計算: 由物理學與功率的關系可知: N=FV/1000 (3-4) 式中 N——功率(kW) F——作用力(N) V——物體在力F作用下的運動速度( m/s ) 顯然對于砂帶磨削來說,上式中 F=Ft(切向磨削力) V=Vs(砂帶磨削速度) 所以,砂帶磨削的功率應為: N= Ft Vs/1000 (kW) (3-5) 因而,由(3-5)計算得: N= Ft
46、 Vs/1000=(35530)/1000=10.65Kw 由于電機在傳輸過程中有必要的功率損失,所以選用電機 Y132S-4 ,其主要技術數(shù)據(jù)如下: 額定功率:15Kw 滿載轉速:1460r/min 起動轉矩額定轉矩:2.2N/m 最大轉矩額定轉矩:2.2N/m 3.1.3 砂帶張緊力計算: Fo= PB (3-6) 式中 P——砂帶張力系數(shù) 50-100/25mm B——砂帶寬度 200mm 由(3
47、-6)計算得: Fo=PB =400-800N 3.1.4 磨頭結構的尺寸設計: ① 接觸輪設計 驅(qū)動輪直徑( D1 )的確定 驅(qū)動輪直徑( D1 )可由下式計算,即 D1=(601000Vs)/πNS (mm) (3-7) 式中 Vs——砂帶速度 30m/s Ns——驅(qū)動輪轉速 r/min 初定驅(qū)動輪直徑 D1 =250mm,可由公式(3-7)得: Ns=(601000Vs)/πD1 =2304 r/min 由于砂帶驅(qū)動電機的滿載轉速 N=1460r/min 由此可得主運動傳動比
48、 i: i=NS/N=2304/1460=1.57 取標準值 i=1.6. 因為設計中選用接觸輪式且驅(qū)動輪為接觸輪,所以接觸輪直徑 D 即為驅(qū)動輪直徑 D1,即 D= D1=250mm 。同時,由于去毛刺的加工性質(zhì)為輕載精加工,因而接觸輪將選用表面為平坦狀的形式,輪材選用呂材,表面材料為橡膠,硬度和密度為 Hs=40-95[9],具體設計見附圖。 ② 張緊輪設計 砂帶必須在一定張緊力作用下才能工作,張緊機構產(chǎn)生的張緊力通過張緊輪使砂帶得以張緊,并在驅(qū)動作用下使砂帶進行磨削,張緊輪不但起張緊砂帶的作用,而且還起導向作用,使砂帶不致偏離接觸輪。張緊輪直徑越大,導向控制越靈敏
49、。一般情況下建議直徑大于 φ125mm。張緊輪過小會引起砂帶彎曲過分或振動,也會使其轉速過高帶來其他不利影響。為使砂帶定心,張緊輪和驅(qū)動輪外圓都要求作成中凸弧形。中凸高度值不能過大,否則會引起砂帶振動及受力不均并使砂帶中部損傷。本設計中,因為 B=200mm,中凸高度值由查閱有關資料得: σ=2mm。 同時為了磨削性能的抱枕,必須讓砂帶有一定的包角,且由于驅(qū)動輪為接觸輪,所以張緊輪直徑 D2應該小于接觸輪直徑 D。 綜上,選定張緊輪直徑 D2=200mm。 3.1.5 砂帶尺寸選擇及計算: 前文提到選用的砂帶為:1950mm200mm(長度寬度)( VSM KK711 422 ),其粒
50、度為 P=120,可以很好的完成加工要求。 由于接觸輪與張緊輪的直徑都已經(jīng)確定,又選定砂帶型號,即已知: D=250mm、D1=200mm、L=1950mm。因而可以計算出帶輪間的中心距d和砂帶的包角a,公式如下: 中心距: d=(L-πDm)/4+()/4 (3-8) 式中 Dm=(D+D2)/2; △=(D-D2)/2; 可得:d=621.2mm 驅(qū)動輪包角: a=180+[(D-D2)60]/d (3-9) 可得: a=184.83 由于包角的大小影響砂帶的傳載能力,包角越大,傳載能力越強,一般
51、來說包角越大越好。若包角過小,傳遞動力時易打滑。計算包角不得小于許用包角值 [a],即 a≥[a] 這在磨頭結構設計時非常重要。驅(qū)動輪面是鋼材或鋁材時取[a]=150,而本設計中a=184.83,滿足條件。 3.1.6 砂帶磨削過程中的受力分析: 上文提到本設計將采用接觸輪式磨削,而接觸輪式磨削是砂帶磨削所有類型中應用最多,也是最有代表性的形式,其結構方式有兩種基本形式:接觸輪直接作為驅(qū)動輪,另一輪子為張緊輪;接觸輪不做驅(qū)動輪,驅(qū)動輪同時又是張緊輪??紤]到機床的總體布局,本設計中將采用接觸輪直接作為驅(qū)動輪的形式。砂帶磨削過程中的砂帶受力分析如下: 當砂帶靜止時,上下兩邊的砂帶張力均為砂
52、帶初張力 F0 。當驅(qū)動輪轉動時,驅(qū)動輪對砂帶的作用力為Ff(有效圓周力)。砂帶與工件接觸產(chǎn)生一定的磨削力,分法向磨削力(Fn)和切向磨削力(Ft),并反作用與砂帶。此時砂帶兩邊的張力發(fā)生變化,分別為F1、F2。在臨界狀態(tài)(即砂帶磨削中將要而又沒有打滑的狀態(tài))時,各種作用力之間存在如下關系: Ff + F1 = Ft + F2 如果不計輪子本身的轉動慣量和輪軸軸承間的摩擦阻力,應有: F1 = F2 ,得Ff = Ft 。 由此可見,欲使砂帶能保持正常磨削而不打滑,必須 Ff > Ft 。 由平帶傳動原理可知,有效圓周力Ff與張緊力 F0 和輪子結構尺寸之間的關系是:
53、 (3-10) 其中 F0 ——砂帶初張力,選 F0 = 400N e——自然對數(shù)的底( e = 2.718...) u——砂帶與驅(qū)動輪接觸面的摩擦系數(shù) a——砂帶繞驅(qū)動輪的有效包角 由此可以得出理論圓周力,而實際圓周力應為: Ff0 = Ff + kuFn (3-11) 式中 k——與接觸弧長和接觸輪開槽情況有關的系數(shù),當接觸輪無開槽時k=1; Fn ——法向磨削力。 最后通過計算得出實際圓周力為:F
54、f0 = 1311 N 3.1.7 張緊機構及快換操縱機構和調(diào)偏機構[10] 為使砂帶磨頭正常傳遞動力,使砂帶正常磨削,砂帶必須張緊。另外,在工作中由于砂帶也會塑形伸長,其預緊力會下降,必須使砂帶重新張緊。 張緊方式有內(nèi)部張緊(張緊輪壓在砂帶背面)與外部張緊(張緊輪壓在砂帶砂面)兩類,本設計中采用的是前者內(nèi)部張緊。此外張緊機構可分為周期性張緊和自動張緊兩類。周期性張緊多采用螺紋和渦輪副等。自動一般采用彈簧、配重及氣動、液壓張緊裝置等。本設計中采用的是彈簧自動張緊裝置,結構見磨頭結構圖。前文張緊輪設計說明中提到,張緊輪通過設計一個中凸值,可以很好地防止砂帶在磨削運動過程中不致于偏離接觸輪,
55、因而不必獨立設計調(diào)偏機構??鞊Q操縱機構主要采用了手柄杠桿原理來簡單實現(xiàn),操作簡單且高效。詳細結構見磨頭機構圖。 3.2 主軸設計[10] ① 選擇軸的材料 選用45鋼,正火處理。估計軸的直徑小于100mm,查的:δb =600Mpa,δs =300Mpa,δ-1=275 Mpa,τ-1=140 Mpa。 ② 所承受的扭矩初估計軸的最小直徑 (3-12) 查的,C =118-107,取 C =118(此軸為轉軸)。則 因最小直徑在帶輪處,此處有一鍵槽,且由于軸的懸伸量較大,故軸徑因適當增大,參照有關經(jīng)
56、驗,取標注值d=26mm。 ③ 軸的結構設計(見圖3-2a) A 確定各段軸的直徑 考慮到軸上接觸輪與皮帶輪分別由軸的兩端裝卸,且皮帶輪處為最小軸徑,接觸輪安裝在軸上需要一定的錐度,且接觸輪處懸伸量較大,所以接觸輪軸頭處軸徑應適當增大,取28mm,為保證一定錐度,到軸頸處取軸徑30mm,即兩端軸徑都取30mm。軸肩處需安裝軸承,軸徑應大于軸頸處軸徑30,同時考慮到滾動軸承內(nèi)徑的標準值,所以軸肩直徑取標準值35mm。軸肩與軸頸過渡處的倒圓半徑取為2mm,軸身軸徑適當增大,取為40mm,軸肩與軸身處退刀槽尺寸為21mm。接觸輪軸端處需螺母固定接觸輪,選用M20螺母,因此此處軸徑為M20。
57、B 初選軸承類型及型號 因軸主要承受徑向載荷,所以選用深溝球軸承,且主軸部件是磨頭的關鍵部件,為了防止軸承磨損后造成較大的徑向跳動,采用雙聯(lián)軸承自行消除軸向間隙的結構,即各自選用一對C級6307軸承,詳情見主軸裝配圖。 C 確定各段軸的長度 軸承間采用套筒進行軸向定位。為保證套筒與軸承端面緊靠定位,且軸承間有定距環(huán),裝軸承處的軸肩長度應略小于兩軸承寬度和定距環(huán)寬度之和,定距環(huán)寬度初定為3mm,所以兩端軸肩處長度取為42mm。帶輪處軸徑由于需安裝端蓋,且到帶輪處需一定的懸伸量,取為80mm。帶輪軸頭長度由帶輪寬度決定,下一節(jié)中將對帶輪設計作詳細介紹,長度取為52mm。由于接觸輪寬度為200
58、mm,有較大懸伸量,且此端軸頸需安裝定距環(huán)和端蓋,定距環(huán)初定為15mm,加上端蓋厚度,此處軸頸長度取為50mm。接觸輪安裝出軸頭,應比接觸輪寬度小,取為150mm,軸端需上一個螺母與墊片固定接觸輪,長度取20mm。軸身長度為86mm。 D 軸上零件的周向固定 帶輪出采用A型普通平鍵聯(lián)接,由手冊查得截面尺寸bh為8mm7mm,長度取為45mm。 E 確定軸上倒圓半徑及軸肩與軸頭表面粗糙度 軸肩與軸頸過渡處的倒圓半徑取為1.5mm,軸頭表面粗糙度 ,軸肩表面粗糙度由軸承標準查得 。 ④ 軸的受力分析 A 求軸上扭矩 =9550=44.1 B 求接觸輪上及帶輪上作用力 由前文知,
59、接觸輪受磨削力與砂帶反作用于它的實際圓周力,分別為:Ff=1311N,F(xiàn)t=355N ,F(xiàn)n =511N 帶輪上的作用力將在下節(jié)作詳細介紹,得 F=1384N C 確定跨距 右端支反力作用點到帶輪作用點間的距離為:=50mm 左端支反力作用點到接觸輪作用點間的距離為:=100mm 兩支反力作用點間的距離為:=213mm D 作計算簡圖(見圖3-2 b ) E 求水平面內(nèi)支反力 及 ,并作水平彎矩 圖(見圖3-2 c、d ) 截面1的彎矩: 截面2的彎矩: F 求垂直面內(nèi)支反力和,并作垂直面彎矩圖(見圖3-2 e、f ) 截面1的彎矩: 截面2的彎
60、矩: G 作合成彎矩M圖(見圖3-2 g ) 截面1的合成彎矩: 截面2的合成彎矩: H 作扭矩T圖(見圖3-2 h ) ⑤ 軸的疲勞強度安全系數(shù)校核計算 確定危險截面:由圖3-2a所示看出,軸上多個截面存在應力集中,但截面3和截面6所受載荷較小,可不考慮。截面4和截面5軸徑相同,但截面4比截面5所受的載荷小,故排除截面4。截面2所受載荷較小,可排除。所以只需對截面1和截面5進行安全系數(shù)校核。 A 截面5的安全系數(shù)校核計算 查得: 有效應力集中系數(shù):=2.52, =1.82 絕對尺寸系數(shù):=0.91,=0.89 表面狀態(tài)系數(shù):=0.85,=1.5,β= =1.2
61、75 等效系數(shù)查得:=0.34,=0.21 截面的抗彎、抗扭截面模量()由軸的直徑d=30mm,查得: 截面上的應力: 彎曲應力為對稱循環(huán)變化,彎曲應力幅: 平均應力0; 扭轉切應力為脈動循環(huán)變化,扭轉切應力: 扭轉切應力幅與平均切應力相等, 安全系數(shù): 彎曲安全系數(shù): 扭轉安全系數(shù): 綜合安全系數(shù): 取[S]=1.0-1.1,S>[S],合適。 B 截面1的安全系數(shù)計算 查得: 有效應力集中系數(shù):=1.86, =1.54 絕對尺寸系數(shù):=0.91,=0.89 表面狀態(tài)系數(shù):=0.93,=1,β= =0.93 等效系數(shù)查得:=0.34,=
62、0.21 截面的抗彎、抗扭截面模量()由軸的直徑 d =26mm,鍵槽寬 b =8 mm, 鍵槽深 t =4 mm ,查得: 截面上的應力: 彎曲應力為對稱循環(huán)變化,彎曲應力幅: 平均應力0; 扭轉切應力為脈動循環(huán)變化,扭轉切應力: 扭轉切應力幅與平均切應力相等, 安全系數(shù): 彎曲安全系數(shù): 扭轉安全系數(shù): 綜合安全系數(shù): 取[S]=1.0-1.1,S>[S],合適。 C 校核鍵聯(lián)接的強度 安裝帶輪需要用一個 A 型普通平鍵來聯(lián)接,軸徑為26 mm ,需對該處鍵聯(lián)接的強度進行校核。 已知:鍵長 L=45mm,工作長度l= L-b = 45mm
63、-8mm = 37mm ,鍵高 h=7mm ,接觸高度 k = h/2 = 7 mm /2 = 3.5 mm 擠壓強度和剪切強度校核: 查得[]=90Mpa,[]=(100-120)Mpa,<[],<[],故合適。 圖3.1 軸的受力計算圖 3.3 帶輪設計[9] 由于主軸采用電機通過帶傳動驅(qū)動,故對主軸帶輪進行必要的設計。已知:傳遞功率 P0 =4.13Kw ,主軸轉速 N =2304r/min,傳動比 i=1.6,一般用途使用時間10年(每年工作250天),雙班制連續(xù)工作,單向運轉,具體設計如下: ⑴ 確定計算功率P 查得工
64、況系數(shù),則 ⑵ 選擇V帶型號 根據(jù)P=11.7kW,n=2304r/min,查手冊得:選用B型。 ⑶ 確定帶輪基準直徑 查手冊得:=125mm,則 ⑷ 驗算帶的速度 <25m/s ⑸ 確定中心距a和V帶基準長度Ld 由0.7(+)≤≤2(+) 即227.5mm=0.7(125mm+200mm)≤≤2(125mm+200mm)=650mm 則初選中心距 =430mm ⑹ 初算 V 帶的基準長度 =1374mm 選取基準長度 =1400mm 實際中心距:
65、 取a=443mm ⑺ 驗算小帶輪上的包角 ,合適 ⑻ 確定V帶根數(shù) 由=125mm,n=2304r/min,查得,B型單根V帶所能傳遞的基本額定功率=2.64kW,功率增量=0.56kW,查得包角系數(shù)=0.98,長度修正系數(shù)=0.90;所需帶的根數(shù) 取 z =5根 ⑼ 確定初拉力 ,查得,A型帶 q =0.17kg/ m,得: ⑽ 確定作用在軸上的壓軸力 ⑾ 帶輪結構尺寸設計(見主軸裝配圖) 4 工作臺設計 在本設計中,磨頭的位置恒定,因此磨削量的控制將通過工作臺的升降來實現(xiàn)。本章將介紹此工作臺的具體設計。 首先,工件的定位
66、與夾緊是通過磁臺來實現(xiàn)的,而工件的進給運動是通過傳送帶來實現(xiàn),在磨削過程中,當加工不同厚度工件的時候,需要調(diào)節(jié)磁臺與磨頭間的位置高度,而實際磨削去毛刺過程中,這個位置高度值就是工件的厚度,所以如何調(diào)節(jié)這個高度值就該由工作臺來實現(xiàn),即工作臺將能夠?qū)崿F(xiàn)上下位置的升降。而摩擦片的厚度往往不是很大,前面機床主要參數(shù)中提到,加工工件厚度范圍為3-20 mm ,即工作臺需要能夠?qū)崿F(xiàn) 17 mm 的微量上下調(diào)節(jié)。為了解決這個問題,設計中將通過一個蝸輪蝸桿傳動與一個絲桿螺母傳動的組合來實現(xiàn)。調(diào)節(jié)過程中通過手動調(diào)節(jié)與蝸桿相連接的手輪控制磨削量,最后通過絲桿的上下移動來完成對工作臺升降的控制(詳細結構見工作臺裝配圖)。對蝸桿傳動和絲桿螺母的設計如下: 由于此傳動只是調(diào)節(jié)磨削量,傳動過程中沒有受到實際載荷,也不需要有轉速控制,因而只需對各傳動的主要結構參數(shù)作出必要設計即可。 4.1 蝸輪蝸桿傳動設計[9] ① 選擇材料與熱處理方式 蝸桿選用 45 鋼,表面淬火處理,齒面硬度 >45 HRC 。蝸輪材料選用ZcuSn10Pb1,砂
- 溫馨提示:
1: 本站所有資源如無特殊說明,都需要本地電腦安裝OFFICE2007和PDF閱讀器。圖紙軟件為CAD,CAXA,PROE,UG,SolidWorks等.壓縮文件請下載最新的WinRAR軟件解壓。
2: 本站的文檔不包含任何第三方提供的附件圖紙等,如果需要附件,請聯(lián)系上傳者。文件的所有權益歸上傳用戶所有。
3.本站RAR壓縮包中若帶圖紙,網(wǎng)頁內(nèi)容里面會有圖紙預覽,若沒有圖紙預覽就沒有圖紙。
4. 未經(jīng)權益所有人同意不得將文件中的內(nèi)容挪作商業(yè)或盈利用途。
5. 裝配圖網(wǎng)僅提供信息存儲空間,僅對用戶上傳內(nèi)容的表現(xiàn)方式做保護處理,對用戶上傳分享的文檔內(nèi)容本身不做任何修改或編輯,并不能對任何下載內(nèi)容負責。
6. 下載文件中如有侵權或不適當內(nèi)容,請與我們聯(lián)系,我們立即糾正。
7. 本站不保證下載資源的準確性、安全性和完整性, 同時也不承擔用戶因使用這些下載資源對自己和他人造成任何形式的傷害或損失。
最新文檔
- 6.煤礦安全生產(chǎn)科普知識競賽題含答案
- 2.煤礦爆破工技能鑒定試題含答案
- 3.爆破工培訓考試試題含答案
- 2.煤礦安全監(jiān)察人員模擬考試題庫試卷含答案
- 3.金屬非金屬礦山安全管理人員(地下礦山)安全生產(chǎn)模擬考試題庫試卷含答案
- 4.煤礦特種作業(yè)人員井下電鉗工模擬考試題庫試卷含答案
- 1 煤礦安全生產(chǎn)及管理知識測試題庫及答案
- 2 各種煤礦安全考試試題含答案
- 1 煤礦安全檢查考試題
- 1 井下放炮員練習題含答案
- 2煤礦安全監(jiān)測工種技術比武題庫含解析
- 1 礦山應急救援安全知識競賽試題
- 1 礦井泵工考試練習題含答案
- 2煤礦爆破工考試復習題含答案
- 1 各種煤礦安全考試試題含答案