畢業(yè)設(shè)計(論文)槽凸輪的加工工藝規(guī)劃及數(shù)控加工
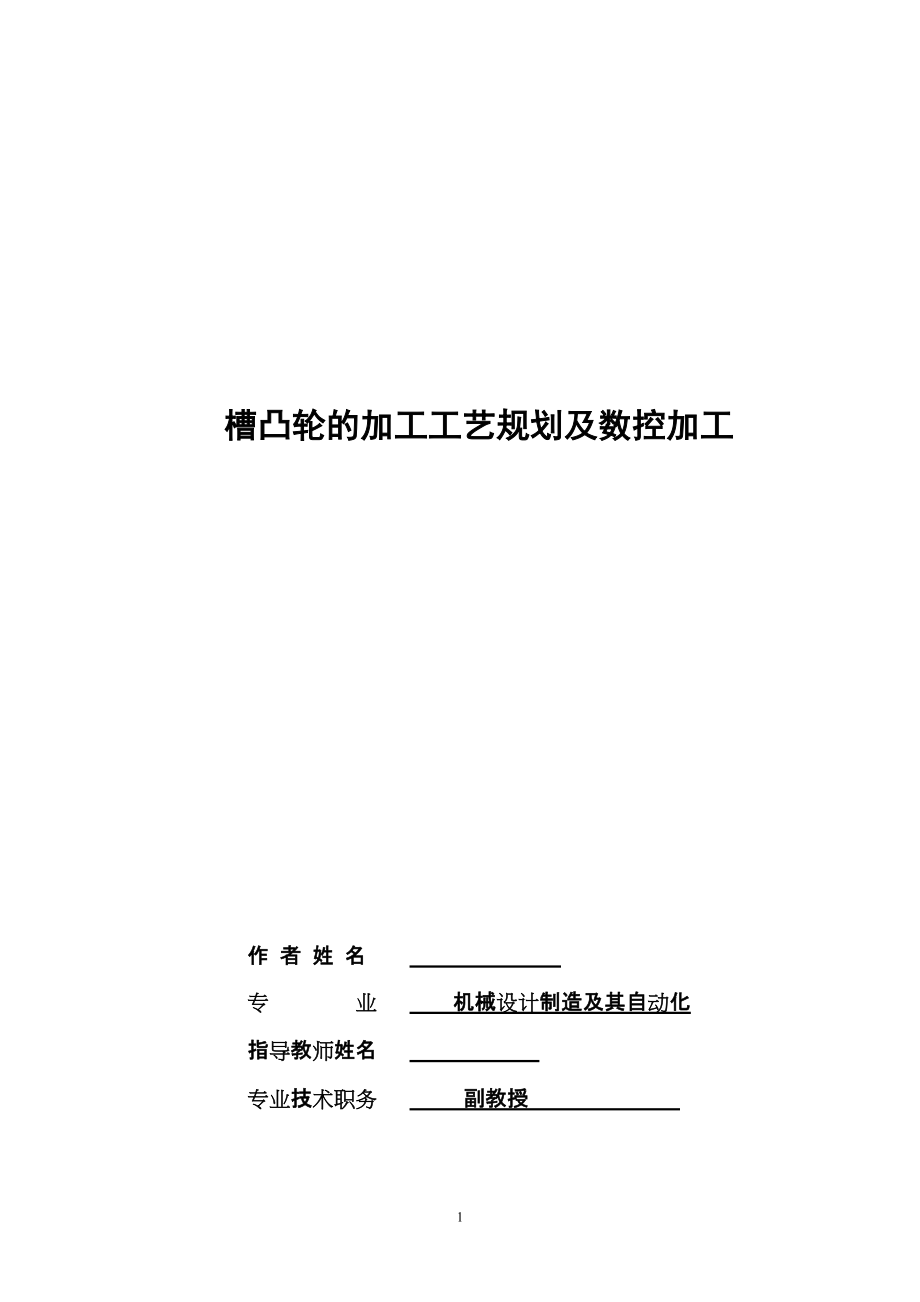


《畢業(yè)設(shè)計(論文)槽凸輪的加工工藝規(guī)劃及數(shù)控加工》由會員分享,可在線閱讀,更多相關(guān)《畢業(yè)設(shè)計(論文)槽凸輪的加工工藝規(guī)劃及數(shù)控加工(21頁珍藏版)》請在裝配圖網(wǎng)上搜索。
1、 槽凸輪的加工工藝規(guī)劃及數(shù)控加工 作 者 姓 名 專 業(yè) 機械設(shè)計制造及其自動化 指導(dǎo)教師姓名 專業(yè)技術(shù)職務(wù) 副教授 目 錄 摘 要 ……………………………………………………………4 第一章 緒論…………………………………………………4 1.1 課題內(nèi)容…………………………………………………………4 1.2 選題意義………………………………………………
2、…………5 1.3 與課題內(nèi)容相關(guān)的現(xiàn)狀及發(fā)展趨勢……………………………5 第二章 零件的工藝分析……………………………………5 2.1 零件的圖樣分析…………………………………………………5 2.1.1 零件的結(jié)構(gòu)特點 ……………………………………………5 2.1.2 零件的技術(shù)條件分析 ………………………………………5 2.2 零件的工藝分析 ………………………………………………6 第三章 毛坯的粗加工………………………………………7 3.1 毛坯的選擇………………………………………………………7 3.1.1 毛坯的種類 ………………………………………
3、…………7 3.1.2 毛坯選擇應(yīng)考慮的因素 ……………………………………7 3.2 加工余量的確定…………………………………………………7 3.2.1 加工余量的概念 ……………………………………………7 3.2.2 影響加工余量的因素 ………………………………………7 3.2.3確定加工余量的方法 …………………………………………8 3.3 毛坯的加工方案 …………………………………………………8 3.3.1 確定毛坯的加工方案 ………………………………………8 3.3.2 確定各工序所用的設(shè)備………………………………………9 3.
4、3.3 表面加工方法的選擇………………………………………9 3.3.4 各工序的切削用量…………………………………………10 第四章 零件的數(shù)控加工…………………………………10 4.1數(shù)控機床 ………………………………………………………10 4.1.1數(shù)控機床簡介 ………………………………………………11 4.1.2數(shù)控加工 …………………………………………………11 4.1.3數(shù)控加工的過程 ……………………………………………12 4.2 零件的數(shù)控加工工藝…………………………………………12 4.2.1確定工藝路線 …………………………………
5、……………11 4.2.2確定各工序所用設(shè)備 ………………………………………11 4.2.3工件的裝夾 …………………………………………………11 4.2.4定位基準(zhǔn)的選擇 ……………………………………………11 4.2.5方案的具體實施 ……………………………………………12 4.3零件的數(shù)控編成 …………………………………………14 4.3.1加工編成概述 ………………………………………………15 4.3.2加工編成的分類 ……………………………………………15 4.3.3程序 ………………………………………………………16 第五章 小結(jié)及
6、參考文獻(xiàn)…………………………………19 摘 要 本文首先進(jìn)行了墻板右內(nèi)凸輪橢圓校訂包本機的工藝分析,規(guī)劃出零件的工藝加工路線:毛坯的粗加工(零件材料的選擇,加工余量的確定等);零件的數(shù)控加工包括工件的工藝方案(外圍輪廓的加工,方孔的加工,中心孔的加工,凸輪槽的加工等)和數(shù)控編程。這就必須介紹數(shù)控機床和數(shù)控加工過程,然后根據(jù)已確定的零件的工藝路線,進(jìn)行數(shù)控編成——用G代碼把零件的各工序用數(shù)控語言編寫出來。期間用到的軟件有:AUTOCAD, PRO/E。最后做一下總結(jié),列出所用到的參考文獻(xiàn)。 關(guān)鍵詞:數(shù)控加工 槽凸輪 ABSTR
7、ACT The first right of the panel wall cam elliptical editing package this aircraft technology analysis, planning out parts of the processing line techniques : blank the rough machining (parts material choice allowance identification, etc.); Parts of the digital processing techniques including wor
8、king programme (external contours of the processing side Kong processing, the processing center Kong, cam shafts processing, etc.) and digital programming. This must be introduced numerically controlled machine tools and digital processing, and then on the basis of the identified parts crafts line,
9、digital organization -- using G code parts of the processes used to prepare digital language out. The software used during : AutoCAD, PRO/E. Finally done it concluded that the use of the references listed. Keywords: Digital processing cam shafts 第一章 緒論 第一節(jié) 課題內(nèi)容 一. 課
10、題類型 本課題屬于工程設(shè)計類,因為我們不但要測繪出零件的具體尺寸,還要根據(jù)零件的結(jié)構(gòu),設(shè)計出它的加工工藝,進(jìn)一步把工藝進(jìn)行數(shù)控編成。 二. 課題主要任務(wù) 本課題主要研究零件的加工工藝及數(shù)控編程,通過對零件圖紙的分析,了解零件的結(jié)構(gòu)及技術(shù)要求,針對零件的類型及生產(chǎn)批量做出合理的加工方案。零件的工藝路線制定以后,應(yīng)參照數(shù)控課本對每一工序進(jìn)行編程。 第二節(jié) 選題意義 通過對槽凸輪數(shù)控加工工藝的分析,對零件的加工過程有了一定的了解,能自行編制出加工工序,不但對四年來所學(xué)的知識進(jìn)行了融會貫通,也為以后參加工作積累了經(jīng)驗。另外學(xué)生通過數(shù)控程序的編制,對數(shù)控機床有了進(jìn)一步的認(rèn)識。 ?。∷邢?/p>
11、載了本文的注意:本論文附有CAD圖紙和完整版word版說明書,凡下載了本文的讀者請加QQ153893706,或留下你的聯(lián)系方式(QQ郵箱)最后,希望此文能夠幫到你! 第三節(jié) 與客體內(nèi)容相關(guān)的現(xiàn)狀及發(fā)展趨勢 數(shù)控機床的發(fā)展趨勢: 目前,世界先進(jìn)制造技術(shù)不斷興起,超高速切削、超精密加工等技術(shù)的應(yīng)用,柔性制造系統(tǒng)的迅速發(fā)展和計算機集成系統(tǒng)的不斷成熟,對數(shù)控加工技術(shù)提出了更高的要求。為適應(yīng)這種情況,數(shù)控機床正朝著以下幾個方面發(fā)展。 1.高速度、高精度化 速度和精度是數(shù)控機床的兩個重要指標(biāo),它直接關(guān)系到加工效率和產(chǎn)品質(zhì)量。 目前,數(shù)控系統(tǒng)采用位數(shù)、頻率更高的處理器,以提高系統(tǒng)的基本運算速
12、度。同時,采用超大規(guī)模的集成電路和多微處理器結(jié)構(gòu),以提高系統(tǒng)的數(shù)據(jù)處理能力,即提高插補運算的速度和精度 2.CAD/CAM圖形交互式自動編程已得到較多應(yīng)用 這是數(shù)控技術(shù)發(fā)展的新趨勢。它是利用CAD繪制的零件加工圖樣,再經(jīng)計算機內(nèi)的刀具軌跡數(shù)據(jù)進(jìn)行計算和后置處理,從而自動生成NC零件加工程序,以實現(xiàn)CAD與CAM的集成。 第二章 零件工藝分析 第一節(jié) 零件的圖樣分析 一. 零件的結(jié)構(gòu)特點 該零件形狀主要由外輪廓,中心孔,方孔和凸輪槽四部分組成,如圖 1 除凸輪槽外,各加工面的幾何形狀很簡單,而且該零件有合理的加工基準(zhǔn),中心孔可以為主要基準(zhǔn),外圍輪廓線過渡很圓滑,這
13、便于零件的加工。 二.零件的技術(shù)條件分析 1.技術(shù)要求 (1) 如圖1,同時加工JBBT 10.07-05和直徑為 47,35 的孔,并保存尺寸260一致,直徑為47和35的孔的軸線要和截面A保持垂直度為0.02的公差,還要同銑周邊和方孔,并在A出打相同的標(biāo)志。 (2) 理論廓線按圖中給定的坐標(biāo)加工,過度時要圓滑,不允許有接痕。 (3) 內(nèi)外工作輪廓線為滾子運動軌跡的包絡(luò)線,滾子外徑22mm (4) 凸輪向徑允差為+-0.05mm (5) 凸輪曲面要進(jìn)行氮化處理,可以獲得表面強度950-1100HV (6) 除孔外,表面噴主機外觀漆。 (7) 全部倒角 2.技術(shù)條件
14、 (1) 軸孔精度 槽凸輪上的軸孔是軸承的支撐孔,該孔不僅本身有較高的尺寸精度,幾何形狀精度,表面粗糙度,而且還有較高的孔距精度和同軸度要求,如果位于同一中心線的若干孔不同軸,將會使軸的裝配發(fā)生困難,如果相鄰孔的中心距偏差較大,或兩孔中心線不平行,就會影響裝配精度。 如圖2 (2) 平面的精度 底面和端面的表面粗糙度都是3.2um,但由于底面的加工面積大,加工時要選擇不同的加工方案,底面對于端面的垂直度為0.02um,應(yīng)先加工地米面再加工端面。 第二節(jié) 零件的工藝分析 1.該工件為盤類零件,它的主要加工部分是外圍輪廓線,中心孔和凸輪槽三部分,為保證他們的加工精度,必須首先保證直
15、徑為47的孔的加工精度。 2.由于板面的長度和壁厚的比值較大,加工時容易產(chǎn)生變形,為了減少孔徑的變形和平面的翹曲,在加工過程中應(yīng)增大夾緊面的面積,建議精銑時采用專用工裝進(jìn)行夾緊工作。 3. 粗加工后進(jìn)行調(diào)質(zhì)處理,再進(jìn)行精加工和銑削加工,可保證加工質(zhì)量的穩(wěn)定。 4.對于銑凸輪槽這個工藝,如果用組合夾具或?qū)S霉ぱb,應(yīng)要求備有槽位置度檢查基準(zhǔn),可供加工時對刀具及加工后檢查使用。 5.凸輪槽銑削時拐角處不能清根,采用鉗工修銼的方法較合適,若不清根,會影響凸輪槽的使用。 6.A-A截面對直徑為35和47內(nèi)孔軸心線的垂直度公差可用偏擺儀進(jìn)行檢測。 7.為了保證加工精度應(yīng)使定位基準(zhǔn)統(tǒng)一,該工
16、件主要定位基準(zhǔn)集中在孔和平面上。 8.孔的尺寸精度檢驗,使用內(nèi)徑千分尺或百分表進(jìn)行測量,同一軸線上個各孔的同軸度,可用檢驗心軸進(jìn)行檢驗。 9.現(xiàn)代加工方法,對此種板料的加工根據(jù)其加工精度,多數(shù)采用數(shù)控火焰切割機或離子切割機進(jìn)行加工,直接切割除凸輪的外輪廓線。 第三章 毛坯的粗加工 第一節(jié) 毛坯的選擇 一. 毛坯的種類 1. 鑄件 加工形狀復(fù)雜的毛坯,表面加工精度高 2. 鍛件 適合加工機械強度要求較高的鋼制件, 3. 焊接件 適
17、于單件小批量生產(chǎn)中制造大型毛坯,優(yōu)點是制造簡便,周期短,毛坯重量輕。 4. 型材 分為熱軋和冷軋,熱軋價格便宜,用于一般零件的毛坯;冷軋的尺寸較小,精度高,多用于批量較大在自動機床上進(jìn)行加工的情況。 5. 沖壓件 沖壓件的尺寸精度高,加工效率高,是與批量較大而零件厚度較小的中小型零件 6. 冷擠壓件 生產(chǎn)效率高,表面粗糙度值小,可以不再進(jìn)行機械加工,是與大批量生產(chǎn)中制造形狀簡單的小型零件。 二. 毛坯選擇應(yīng)考慮的因素 1.零件的材料及對零件力學(xué)性能的要求 零件的材料如果是青銅或鑄鐵,只能選鑄造毛坯,不能選鍛造,當(dāng)材料的力學(xué)性能要求較高時,不管形狀簡單與復(fù)雜,都應(yīng)選鍛
18、件,該零件對材料的力學(xué)性能無過高要求,所以選型材。 2.零件的結(jié)構(gòu)形狀與外形尺寸 加工零件的臺階若直徑相差不大,可用棒料,若臺階直徑相差大,則宜用鍛件,以節(jié)約材料,減少機械加工工作量。大型零件,受設(shè)備條件限制,一般只能用自有段和砂型鑄造。中小型零件根據(jù)需要可選用模鍛和各種先進(jìn)鑄造方法。 3.生產(chǎn)類型 大批量生產(chǎn)時,應(yīng)選毛坯精度和生產(chǎn)率都高的先進(jìn)毛坯制造方法,是毛坯的形狀、尺寸盡量接近零件的形狀、尺寸,以節(jié)約材料,由此所節(jié)約的費用會遠(yuǎn)遠(yuǎn)超出毛坯制造所增加的費用,獲得好的經(jīng)濟效益。單件小批量生產(chǎn)時,應(yīng)選用毛坯精度和生產(chǎn)率比較低的一半毛坯制造方法,如自由段和手工木模造型等方法。 4.生產(chǎn)條
19、件 選擇毛坯時應(yīng)考慮現(xiàn)有生產(chǎn)條件,如現(xiàn)有毛坯制造水平和設(shè)備情況,外協(xié)的可能性等??赡軙r,應(yīng)盡可能組織外協(xié),實現(xiàn)毛坯制造的社會專業(yè)化生產(chǎn),以獲得好的經(jīng)濟效益。 第二節(jié) 加工余量的確定 一. 加工余量的概念 加工余量是指加工過程中從加工表面所削去的金屬層厚度,它由工序余量和加工總余量之分。工序余量是指某一工序所切除的金屬層厚度,即相鄰的工序尺寸之差;技工總余量是指某加工表面上切除的金屬層總厚度,即毛坯尺寸與零件圖設(shè)計尺寸之差。 二. 影響加工余量的因素 1. 粗糙度Ra和表面缺陷層D 為了保證加工質(zhì)量,此工序必須將上工序留下來的表面粗糙度 ,以及由于切削加工而在表面留下的一層組
20、織已遭破壞的塑性變形層全部切除。 2. 上工序的尺寸公差T 由于工序尺寸有公差,上工序的實際工序尺寸有可能出現(xiàn)最大或最小極限尺寸。為了使上工序的實際工序尺寸在極限尺寸的情況下,本工業(yè)能將上工序留下的表面粗糙度和缺陷層切除,本工序的加工余量應(yīng)包括上工序的公差。 3. 工件各表面相互位置的空間偏差 工踐上有些形狀和位置偏差不包括在尺寸公差之內(nèi),但這些誤差又必須在本工序的加工中糾正,在本工序加工余量中必須包括他。 4. 本工序的裝夾誤差 如果本供需有裝夾誤差是是工件在加工時位置為之發(fā)生偏移,本工序加工余量應(yīng)考慮這些誤差的影響。 二. 確定加工余量的方法 1. 查表法 根據(jù)各
21、工廠長期的生產(chǎn)實踐與試驗研究所積累的有關(guān)加工余糧資料,制成各種表格并匯編成手冊,如機械加工工藝手冊,工藝設(shè)計手冊等。卻定加工余量時,查閱這些手冊,在根據(jù)本廠的實際情況進(jìn)行適當(dāng)修訂后確定。 2.經(jīng)驗估計法 技術(shù)人員根據(jù)工廠的生產(chǎn)技術(shù)水平,靠經(jīng)驗來確定加工余量。為防止圓余量不足而產(chǎn)生廢品,通常所取得加工余量都偏大,此法一班用于單件小批生產(chǎn)。 3.計算法 應(yīng)用上述加工余量計算公式通過計算確定加工余量。此法必需要有可靠的實際數(shù)據(jù)資料,目前應(yīng)用較少。 因為我們是單件小批量生產(chǎn),加工精度要求又不是很高,所以采用經(jīng)驗估計法來確定加工余量。 三. 根據(jù)上述條件我們選擇毛坯時選型材中的板材,并
22、且板材的厚度應(yīng)該是25mm,因為在切割零件時,毛坯容易產(chǎn)生內(nèi)應(yīng)力和熱變形所以一邊應(yīng)留出2.5mm的加工余量。使毛坯成型的方法有:火焰切割、等離子切割、激光切割。等離子加工精度高,適合大批量生產(chǎn);火焰切割在生活中比較常見,費用低,但機械加工工作量大;激光切割加工精度不如等離子切割,不用接觸工件,但費用高。因為我們是單件生產(chǎn),而且生產(chǎn)條件較差,沒有很高的加工精度,所以我們選火焰切割。切割形狀如圖所示 端面留出5mm的加工余量。火焰切割完后,要進(jìn)行退火處理,是工件 硬度達(dá)到16-21HRC,退火是將金屬和合金加熱到適當(dāng)溫度,保溫一定時間 ,然后慢慢冷卻的熱處理工藝,退火可分為:完全退火,球
23、化退火,去應(yīng)力退火,在這里我們?yōu)榱巳コ鹧媲懈詈蟮乃苄宰冃危约靶筒膬?nèi)存在的殘余應(yīng)力,所以選擇去應(yīng)力退火。 第三節(jié) 毛坯的加工方案 一. 確定毛坯表面加工方案 該零件的主要平面的粗糙度要求為Ra3.2um,平面度誤差要求小于0.02mm,宜選用粗銑——粗磨——精磨的加工方案。 二. 確定各工序所用的設(shè)備,刀具,夾具,量具和輔助工具 1.機床的選擇 選擇機床的原則: (1)機床規(guī)格應(yīng)與零件外形尺寸相適應(yīng)。 (2)機床的精度應(yīng)與工序要求的加工精度相適應(yīng) (3)機床的生產(chǎn)率應(yīng)與零件的生產(chǎn)類型相適應(yīng)。 (4)與現(xiàn)有設(shè)備條件相適應(yīng)。 綜合上述各種因素,我們選擇立式銑床來進(jìn)行毛坯表
24、面的加工 2.刀,夾,量具的選擇 (1) 刀具的選擇 一般采用標(biāo)準(zhǔn)刀具,中批以上生產(chǎn)時,可采用高效率的復(fù)合刀具及有關(guān)專用刀具。刀具的類型、規(guī)格即精度等級應(yīng)符合加工要求。在這里我們選擇面銑刀,因為面銑刀主要用于加工臺階面和平面,特別適合較大平面的加工,用面銑刀加工平面,同時參加銑削的刀齒較多,又有副切削刃的修光作用,使加工表面粗糙度值小,因此可以用較大的切削用量 (2) 夾具的選擇 單件小批生產(chǎn)時,應(yīng)盡可能采用通用夾具,為提高生產(chǎn)效率,亦可采用族和家具。中批以上生產(chǎn)時,應(yīng)采用專用家具,以提高生產(chǎn)效率,夾具的精度應(yīng)予工序的加工精度相適應(yīng)。 我們采用如圖所示夾具來夾緊毛坯
25、 在工件的四周用4個頂尖頂緊,而且要盡量布置得勻稱,以提高加工精度。 (3) 量具的選擇 單件小批生產(chǎn)時,應(yīng)盡可能選擇通用量具,大批量生產(chǎn)時應(yīng)廣泛采用各種專用量具和檢具,量具的精度等級應(yīng)與被測工件的加工精度相適應(yīng)。 三. 表面加工方法的選擇 1.銑削 銑削是加工平面的一種主要加工方法,通過合理的選用銑刀和銑床附件,銑削不僅可以加工平面、溝槽、成型面、臺階,還可以進(jìn)行切斷和刻度加工。銑削的另一個優(yōu)點是生產(chǎn)效率高,銑削時,同時參加得刀齒多,進(jìn)給速度快 ,銑削的主運動是的旋轉(zhuǎn),有利于進(jìn)行高速切削。另外,銑削的刀齒散熱條件好,由于是間斷切削,每個刀齒依次參加切削,在
26、切離工件的一段時間內(nèi),刀齒可以得到冷卻,有利于減少銑刀的磨損,延長使用壽命。 銑削有粗銑和精銑、順銑和逆銑之分,加工毛坯時我們選擇粗銑、順銑,順銑是刀齒的切削厚度逐漸減至零,沒有逆銑時的滑行現(xiàn)象,冷硬程度大為減輕以加工表面質(zhì)量高,工件表面無硬皮等缺陷 ,耐用度比逆銑高,粗銑將工件厚度銑至21mm,工件銑完后,接下來要進(jìn)行磨削。 2.磨削 平面磨削有周磨和端磨兩種方式。周磨:利用砂輪的圓柱面進(jìn)行磨削,砂輪與工件的接觸面積小,且排屑和冷卻條件好,工件發(fā)熱小,磨粒與磨屑不易落入砂輪與工件之間,因而能獲得較高的加工質(zhì)量,適合于工件的精磨,但生產(chǎn)率較低;端磨:利用砂輪的端面進(jìn)行磨削,磨床主軸受壓
27、力,剛性好,可以采用較大的磨削用量,另外砂輪與工件的接觸面大,同時參加切削的磨粒多,因而生產(chǎn)率高。但由于磨削過程中發(fā)熱量大,冷卻、散熱條件差、排屑困難,所以加工質(zhì)量較差,只適于粗磨。 工件的磨削先用端磨的方式將一面磨削掉o.45mm,使再磨另一面是工件的厚度達(dá)到20.10mm,然后用周磨的方式多次磨削至20mm,磨削時必須兩個面同時磨,才能保證加工精度。 四. 各工序切削用量 1. 切削速度 銑削速度一般指銑刀最大直徑處的線速度,計算式為 式中d為銑刀直徑 n為銑刀主軸轉(zhuǎn)速 用標(biāo)尺測出刀頭直徑,再調(diào)整好主軸轉(zhuǎn)速,確定出銑削速度為20m每分鐘 2. 進(jìn)給量 銑削是工件在
28、進(jìn)給運動方向上相對刀具的移動量 ,即為銑削時的進(jìn)給量,粗銑時,一般選區(qū)較大的背吃刀量和側(cè)吃刀量,使每一次進(jìn)給盡可能多的切除毛坯余量,以提高加工效率,在這里我們選擇進(jìn)給量為0.12-0.20mm/r. 第四章 零件的數(shù)控加工 第一節(jié) 數(shù)控機床 1.?dāng)?shù)控機床的組成 數(shù)控機床是裝有程序控制系統(tǒng)(數(shù)控系統(tǒng))的機床,是典型的數(shù)控化設(shè)備,他一般由信息載體、計算機數(shù)控系統(tǒng)、伺服系統(tǒng)和機床絲部分組成。 2.?dāng)?shù)控技術(shù)簡介 數(shù)控技術(shù)是綜合機械加工技術(shù)、自動化技術(shù)、計算機技術(shù)、測量技術(shù)和微電子技術(shù)而形成的一門邊緣學(xué)科。數(shù)控技術(shù)是CIMS到FA(無人工廠)的基礎(chǔ)技術(shù),也是當(dāng)今世界機械制造業(yè)的核
29、心技術(shù)。數(shù)控系統(tǒng)是一種采用數(shù)控技術(shù)的控制系統(tǒng),他自動輸入載體上事先給定的數(shù)字量,并將其譯碼,再進(jìn)行必要的信息處理和運算后,控制機床動作和加工運動。最初的數(shù)控系統(tǒng)是由數(shù)字邏輯電路構(gòu)成的專用硬件數(shù)控系統(tǒng)。隨著計算機技術(shù)的發(fā)展,硬件數(shù)控系統(tǒng)已逐漸被淘汰,取而代之的是計算機數(shù)控系統(tǒng)(Computer Numerical Control)簡稱CNC。CNC系統(tǒng)是由計算機承擔(dān)數(shù)控重的命令發(fā)生器和控制器的數(shù)控系統(tǒng)。由于計算機可完全由軟件來確定數(shù)字信息的處理過程,從而具有真正的“柔性”,并可處理硬件邏輯電路難以處理的復(fù)雜信息,使數(shù)字控制系統(tǒng)的性能大大提高。數(shù)控的對象是多種多樣的,但數(shù)控機床是最早應(yīng)用數(shù)控技術(shù)的
30、控制對象。 3.?dāng)?shù)控加工 (1) 定義 數(shù)控加工,就是在對工件材料進(jìn)行加工前,事先在計算機上編寫好程序,再將這些程序輸入到使用計算機程序控制的機床進(jìn)行指令性加工,或者直接在這種使用計算機程序控制的機床控制面板上編寫指令進(jìn)行加工。 (2) 特點 高速度,高精度化 速度和精度是數(shù)控系統(tǒng)的兩個重要指標(biāo),它直接關(guān)系刀加工效率和產(chǎn)品質(zhì)量;高可靠性 數(shù)控機床的工作環(huán)境比較惡劣,又必須抵抗電網(wǎng)電壓波動和干擾,因此對CNC的可靠性要求要高于一般的計算機;多功能化 一臺多功能數(shù)控機床,可以先讀的提高設(shè)備的利用率。數(shù)控加工中心便是一種能凸顯多工序加工的數(shù)控機床。數(shù)控加工中心一般配備機器手
31、和刀具庫。工件已經(jīng)裝夾,數(shù)控系統(tǒng)就能控制機床自動換刀,連續(xù)對工件的各個加工面自動的完成多中加工工序。多道工序一次裝夾,避免造成定位誤差,減少設(shè)備數(shù)量,節(jié)省占地面積和輔助時間,提高了勞動生產(chǎn)率。 4.?dāng)?shù)控加工的過程 零件信息 CAD系統(tǒng)造型 CAM系統(tǒng)生成加工代碼 數(shù)控機床 零件 第二節(jié) 零件的數(shù)控加工工藝 一.確定工藝路線 銑外圍輪廓線 銑方孔 加工中心孔 銑凸輪槽 鉆孔,擴孔 二. 確定各工序所用設(shè)備 1.機床的選擇 因為槽凸輪的加工表面比較大,而且我們又是小批量生產(chǎn),根據(jù)現(xiàn)有設(shè)備條件,我們選擇韓國產(chǎn)的
32、DAWU型號的機床。所有工序都在它上面完成。 2.刀具,量具的選擇 (1)刀具的選擇 在銑外圍輪廓線和方孔時時,我們選擇立式銑刀;在加工槽時選擇圓柱銑刀;在加工中心孔時,我們先用麻花鉆鉆孔,然后用圓柱銑刀進(jìn)行擴孔加工。 (2)量具的選擇 在整個加工過程中,我們用到的量具有游標(biāo)卡尺、螺旋測微器、內(nèi)徑百分表、千分尺。 三. 工件的裝夾 1.工件裝夾的概念 工件在開始前,首先必須時工件在機床上或夾具中占有某一正確位置,這個過程稱為定位。為了使定位好的工件不至于在切學(xué)力的作用下發(fā)生位移,使其在加工過程中始終保持正確的位置,還需要將工件壓緊夾牢,這個過程稱為夾緊。定位和夾緊的整個過
33、程和起來稱為裝夾。 2.夾緊方式 具體方式在 五 中有介紹 四. 定位基準(zhǔn)的選擇 1.基準(zhǔn)分類 (1)設(shè)計基準(zhǔn) 零件圖上用以確定零件上某些點、線、面位置所依據(jù)的點、線、面。 (2)工藝基準(zhǔn) 零件加工與裝配過程中所采用的基準(zhǔn)。 (3) 測量基準(zhǔn) 工件在加工中或加工后測量時所用基準(zhǔn)。 (4) 裝配基準(zhǔn) 裝配時,用以確定零件在部件或產(chǎn)品中的相對位置所采用的基準(zhǔn)。 2.定位基準(zhǔn)的選擇 (1) 粗基準(zhǔn)選擇原則 選擇粗基準(zhǔn)時重點考慮如何保證各個加工面都能分配到合理的加工余量,保證加工面與不加工面的位置尺寸和位置精度,同時還要為后續(xù)工序提高可靠精基準(zhǔn)。具體選擇一般應(yīng)遵循下列原
34、則:為保證零件各加工面都能分配到足夠的加工余量,應(yīng)選加工余量最小的面為精基準(zhǔn);為了保證零件上加工面與不加工面的相對位置要求,應(yīng)選不加工面為粗基準(zhǔn);為了保證零件上重要表面加工余糧均勻,應(yīng)選重要表面為粗基準(zhǔn);粗基準(zhǔn)應(yīng)盡量避免重復(fù)使用。 (2) 精基準(zhǔn)選擇原則 基準(zhǔn)重合原則 所謂基準(zhǔn)重合原則是指以設(shè)計基準(zhǔn)為定位基準(zhǔn),以避免產(chǎn)生基準(zhǔn)不重合誤差;基準(zhǔn)統(tǒng)一原則 黨齡件上有許多表面需要進(jìn)行多道工序加工時,應(yīng)盡可能在各工序的加工中選擇統(tǒng)一組基準(zhǔn)定位;自衛(wèi)基準(zhǔn)原則;互為基準(zhǔn)原則;裝夾方便原則。 至于選用何種基準(zhǔn),在 五(方案的具體實施)中會有詳細(xì)介紹。 五. 方案的具體實施 1.外圍輪廓線的加
35、工 (1)加工方式的選擇 :根據(jù)材料的形狀和端面的加工精度,我們選擇銑削加工中的順銑法進(jìn)行加工 (2)刀具的選擇及走刀方式:選用立式銑刀,按輪廓線進(jìn)行走刀如圖3 (3) 加工余量的確定:如圖所示 (4) 切削用量的確定:材料為45號鋼,所以粗銑時銑削速度為120m每分鐘,進(jìn)給量為0.15mm每轉(zhuǎn)精銑時,銑削速度為150m每分鐘;進(jìn)給量為 0.05mm每轉(zhuǎn). (5) 加工步驟 :用立式銑刀對零件的外圍輪廓線進(jìn)行粗加工,因為材料比較厚,為保證刀具的壽命,應(yīng)進(jìn)行多次走刀。端面往里進(jìn)刀4mm,留出1mm進(jìn)行精加工,第一次走刀將那4mm的工件厚度銑至15mm,銑削速度為120mm每分鐘,進(jìn)給
36、量為0.15mm每轉(zhuǎn),第二次將工件待加工部分厚度銑至10mm,進(jìn)給速度為100mm每分鐘,其余和第一次相同。第三次將工件待加工部分銑至5mm,進(jìn)給速度為90mm每分鐘,第四次加工要把刀具的高度考慮在內(nèi),所以應(yīng)下刀5.5mm,這樣粗加工完畢,下面進(jìn)行精加工,端面往里進(jìn)刀0.99mm,每次走刀深度和粗加工相同,不同的是銑削速度,因為精加工切削量少,所以速度要比粗加工快,第一次走刀切削速度為150mm每分鐘,往后依次減少20mm每次走刀。 2.方孔的加工 0.01mm 對于方孔的加工,我們也是采用銑削的方式,選用刀具也是圓柱銑刀,加工余量如上圖所示,為0.01m
37、m,加工步驟:先進(jìn)行粗加工,然后再進(jìn)行精加工。在進(jìn)行銑削前,要先在方孔的位置鉆一孔,這樣便于下刀。第一次走刀,刀具往下進(jìn)5mm,方孔處的工件厚度銑至15mm,切削速度是200mm每分鐘,進(jìn)給量為0.2mm每轉(zhuǎn),第二次走刀,將工件銑至10mm,切削速度為180mm每分鐘,第三次走刀,將工件銑至5mm,切削速度為150mm每分鐘,最后一次走刀,刀具再往下進(jìn)5.4mm,也是考慮到刀頭高度的因素,這樣才能銑削完全,切削速度為120mm每分鐘。粗銑完之后,在進(jìn)行一遍精銑,進(jìn)給量很小就可以,這樣方孔就加工完畢。 3.中心孔的加工 圓柱銑刀,切削余量如圖所示 對于中心孔的加工,我們采用先鉆后銑
38、的方法,選用刀具有麻花鉆和圓柱銑刀。 加工步驟:先加工直徑為47的孔,用麻花鉆在工件上試鉆一下,鉆一小點,便于下鉆,然后開始鉆孔,鉆頭每下5mm,便往上提升一下,這樣能很好的散熱,使鉆頭不易膠著。麻花鉆頭直徑要比銑刀頭直徑稍大,這樣便于下刀,用圓柱銑刀先粗銑孔的直徑為46.5,第一次走刀,銑5mm厚的加工量,將孔銑至5mm深,切削速度為120mm每分鐘,進(jìn)給量為0.15mm每轉(zhuǎn);第二次走刀,將孔銑至10mm深,銑削速度是100mm每分鐘,進(jìn)給量為0.18mm每轉(zhuǎn),第三次走刀,將孔銑至15mm深,銑削速度為90mm每分鐘,進(jìn)給量為0.20mm每轉(zhuǎn);最后一次走刀,將孔銑至20mm深,考慮刀刀頭的
39、高度,要將刀具往下進(jìn)給到20.5mm,這樣才能把孔加工完整而沒有殘余量。粗加工以后,要進(jìn)行精銑,根據(jù)孔的上下偏差,將孔加工到直徑為46.975mm, 每次進(jìn)給深度和精加工相同,第一次精銑,銑削速度為300mm每分鐘,以后依次減少30mm每分鐘。將孔精加工完,再進(jìn)行兩個小密封槽的加工,首先將圓柱銑刀下刀2.5mm,在孔中試切一下,再將刀具下刀1.7mm,期間加工槽的直徑至49mm,再將刀具下至15.8mm,開始加工另一密封槽,加工槽的深度至1.7mm,直徑為49mm.加工完密封槽后,接著加工直徑為35的孔,并保持兩孔之間的距離260mm,直徑為35的孔的加工基本上與直徑為47的孔的加工相同,只
40、不過粗銑將孔的直徑銑至34.5mm,精銑將孔的直徑銑至34.975mm. 4. 凸輪槽的加工 對于凸輪槽的加工,我們選用銑削的方法,所用刀具為立式銑刀,因為槽的寬度為22mm,所選刀具的寬度為12mm,所以應(yīng)兩次走刀。首先用立式銑刀進(jìn)行試銑,看到加工軌跡正確無誤后,再進(jìn)行粗加工。第一次走刀將槽銑至5mm深,因為槽的形狀表較復(fù)雜,所以切削速度要小一點,設(shè)為120mm每分鐘,進(jìn)給量為0.12mm每轉(zhuǎn),銑完一圈后,精靠著刀具外沿所銑的軌跡再銑一遍,這樣槽的寬度才能達(dá)到22mm。第二次走刀將槽的深度銑至10mm深,切削速度為100mm每分鐘,進(jìn)給量為0.10m每轉(zhuǎn)。第三次走刀將槽的深度銑至13.5
41、mm,切削速度為90mm每分鐘,進(jìn)給量為0.10mm每轉(zhuǎn)。粗加工完畢后,再進(jìn)行精加工,切削速度為200mm每分鐘,進(jìn)給量為0.05mm每轉(zhuǎn),將槽銑至14mm深,測量刀頭的高度為0.45mm,所以精銑時要將刀具下至14.45mm,這樣才能夾槽加工完整,而沒有余量。 5. 鉆孔 對于M12-7H通孔,我們采用鉆——擴——鉸的加工方案,選用直徑為10.9mm的鉆頭,在工件上鉆孔的直徑到11mm,然后用直徑為11.5mm的鉆頭擴孔至11.85mm,然后用鉸刀粗鉸至11.9mm,最后精鉸至12H7。對于M10-8的錐銷孔,我們選用直徑為9.7mm的鉆頭先鉆一個直徑為9.8mm的孔,然后再用鉸刀鉸至1
42、0H8,由于該鉆頭直徑比較小,所以加工時鉆頭的轉(zhuǎn)速不應(yīng)太高,以免是刀頭折斷。鉆孔時,因為零件太厚,不能一下鉆刀底,那樣刀頭容易發(fā)熱,發(fā)生膠著,應(yīng)該每鉆5mm深把刀頭往上提一下。 6.輔助工序 (1)熱處理 各工序加工完以后,要對零件進(jìn)行熱處理。常用的熱處理方法有退火,正火,回火。在這里我們選擇回火處理,目的是穩(wěn)定組織,減少內(nèi)應(yīng)力,降低脆性,獲得所需性能。 (2)去毛刺 檢查各加工面是否光滑,遇到毛刺用小銼合沙紙打磨。 第三節(jié) 零件的數(shù)控編程 一.加工編程概述 將加工零件的加工順序,工件與刀具相對運動軌跡的尺寸數(shù)據(jù),工藝參數(shù)以及輔助操作等加工信息,用規(guī)定的文字、數(shù)字、符號組成
43、的代碼,按一定的格式編寫成加工程序單,并將程序單的信息通過控制介質(zhì)輸入到數(shù)控裝置由數(shù)控裝置控制機床進(jìn)行自動加工。 二. 加工編程的分類 加工編程包括手工編程和自動編程,手工編程整個程序的編制是由人工完成的;而自動編程,工程人員只要根據(jù)零件紙的要求,按照某個自動編程系統(tǒng)的規(guī)定,編寫一個零件源程序,送入到計算機,由計算機自動完成。 三. 程序: % O G90 G54 G40 T01 M06 S600 M03 G43 H01 M03 G01 Z100 F3000 X0 Y-88.73 Z25 F1000 Z22 F60 Z6.1 F40 Z100 F5000
44、 T03 M06 S500 M03 G43 H03 M03 G01 Z100 F3000 X0 Y-88.73 Z25 F1000 Z22 F60 Z6.1 F40 Z100 F5000 T04 M06 S500 M03 G43 H03 M03 G01 Z100 F3000 Z25 F1000 Z15 F60 M98 P Z10 F60 M98 P Z7.5 F30 Z6 F15 M98 P Z100 F5000 T06 M06 S630 M03 G43 H03 M03 G01 Z100 F3000 X0 Y-88.73
45、 Z10 F1000 Z4.2 F100 Z4 F20 M98 P M98 P G01 Z100 F5000 M30 % % O N40 G01 X7.8285 Y-88.0728 F50 N70 G03 X2.4996 Y-85.8436 I-5.1251 J-4.7678 N80 G02 X0.0 Y-85.88 I-2.4996 J85.8436 N90 X-83.4546 Y-20.2656 I0.0 J85.88 N100 X57.3915 Y63.8873 I83.4546 J20.2656 N110 X64.4301 Y52.4796 I-
46、15.8715 J-17.668 N120 X65.936 Y26.0088 I-61.3701 J-16.7696 N130 G03 X65.6937 Y19.5374 I27.7319 J-4.2787 N140 X73.9605 Y7.9263 I13.8076 J1.0823 N150 G01 X77.5801 Y6.3463 N160 G02 X85.136 Y-5.4473 I-5.0401 J-11.5463 N170 X80.3001 Y-30.451 I-74.6356 J1.4654 N180 X-2.4996 Y-85.8436 I-80.3001 J30.
47、451 N190 G03 X-7.9665 Y-88.2255 I-.2038 J-6.997 N40 G01 G90 X-7.9565 Y-88.734 N70 G03 X-2.4997 Y-91.5959 I5.6478 J4.1355 N80 X0.0 Y-91.63 I2.4997 J91.5959 F70 N90 X85.6765 Y-32.4899 I0.0 J91.63 N100 X90.8849 Y-5.5602 I-75.1761 J28.508 N110 X79.8805 Y11.6161 I-18.3449 J.3602 N120 G01 X76.
48、2608 Y13.1961 N130 G02 X71.4261 Y19.9867 I3.2405 J7.4236 N140 X71.6188 Y25.132 I22.2418 J1.7434 N150 G03 X69.9767 Y53.9953 I-68.5588 J10.578 N160 X61.2341 Y68.1648 I-28.4567 J-7.776 N170 X2.4997 Y-91.5959 I-61.2341 J-68.1648 N180 X7.8236 Y-88.9097 I-.191 J6.9974 G01 X0 Y-88.73 M99 % %
49、 O N40 G01 G90 X7.8284 Y-87.9222 N70 G03 X2.4996 Y-85.6936 I-5.1247 J-4.7684 N80 G02 X0.0 Y-85.73 I-2.4996 J85.6936 N90 X-83.3089 Y-20.2302 I0.0 J85.73 N100 X57.2913 Y63.7757 I83.3089 J20.2302 N110 X64.2854 Y52.4401 I-15.7713 J-17.5564 N120 X65.7878 Y26.0317 I-61.2254 J-16.7301 N130 G03 X6
50、5.5441 Y19.5257 I27.8801 J-4.3016 N140 X73.9005 Y7.7888 I13.9572 J1.094 N150 G01 X77.5201 Y6.2088 N160 G02 X84.986 Y-5.4444 I-4.9801 J-11.4088 N170 X80.1599 Y-30.3979 I-74.4856 J1.4625 N180 X-2.4996 Y-85.6936 I-80.1599 J30.3979 N190 G03 X-7.9666 Y-88.0752 I-.2041 J-6.997 N40 G01 G90 X-7.956
51、5 Y-88.8344 N70 G03 X-2.4997 Y-91.6959 I5.6476 J4.1359 N80 X0.0 Y-91.73 I2.4997 J91.6959 N90 X85.77 Y-32.5253 I0.0 J91.73 N100 X90.9848 Y-5.5622 I-75.2696 J28.5434 N110 X79.9205 Y11.7077 I-18.4448 J.3622 N120 G01 X76.3008 Y13.2878 N130 G02 X71.5258 Y19.9946 I3.2005 J7.3319 N140 X71.7176 Y25
52、.1168 I22.1421 J1.7355 N150 G03 X70.0732 Y54.0216 I-68.6576 J10.5932 N160 X61.301 Y68.2392 I-28.5532 J-7.8023 N170 X2.4997 Y-91.6959 I-61.301 J-68.2392 N180 X7.8237 Y-89.0099 I-.1908 J6.9974 M99 % # N10 G40 G17 G94 G90 G70 N20 G91 G28 Z0.0 :30 T00 M06 N40 G00 G90 X7.8284 Y-87.9222 M03
53、 N50 G43 Z2.54 N60 G01 Z0.0 F250. M08 N70 G03 X2.4996 Y-85.6936 I-5.1247 J-4.7684 N80 G02 X0.0 Y-85.73 I-2.4996 J85.6936 N90 X-83.3089 Y-20.2302 I0.0 J85.73 N100 X57.2913 Y63.7757 I83.3089 J20.2302 N110 X64.2854 Y52.4401 I-15.7713 J-17.5564 N120 X65.7878 Y26.0317 I-61.2254 J-16.7301 N130 G0
54、3 X65.5441 Y19.5257 I27.8801 J-4.3016 N140 X73.9005 Y7.7888 I13.9572 J1.094 N150 G01 X77.5201 Y6.2088 N160 G02 X84.986 Y-5.4444 I-4.9801 J-11.4088 N170 X80.1599 Y-30.3979 I-74.4856 J1.4625 N180 X-2.4996 Y-85.6936 I-80.1599 J30.3979 N190 G03 X-7.9666 Y-88.0752 I-.2041 J-6.997 N200 M02 N40
55、 G01 G90 X-7.9565 Y-88.734 N70 G03 X-2.4997 Y-91.5959 I5.6478 J4.1355 N80 X0.0 Y-91.63 I2.4997 J91.5959 N90 X85.6765 Y-32.4899 I0.0 J91.63 N100 X90.8849 Y-5.5602 I-75.1761 J28.508 N110 X79.8805 Y11.6161 I-18.3449 J.3602 N120 G01 X76.2608 Y13.1961 N130 G02 X71.4261 Y19.9867 I3.2405 J7.4236 N1
56、40 X71.6188 Y25.132 I22.2418 J1.7434 N150 G03 X69.9767 Y53.9953 I-68.5588 J10.578 N160 X61.2341 Y68.1648 I-28.4567 J-7.776 N170 X2.4997 Y-91.5959 I-61.2341 J-68.1648 N180 X7.8236 Y-88.9097 I-.191 J6.9974 N40 G01 G90 X-7.9565 Y-88.8344 N70 G03 X-2.4997 Y-91.6959 I5.6476 J4.1359 N80 X0.0 Y-91
57、.73 I2.4997 J91.6959 N90 X85.77 Y-32.5253 I0.0 J91.73 N100 X90.9848 Y-5.5622 I-75.2696 J28.5434 N110 X79.9205 Y11.7077 I-18.4448 J.3622 N120 G01 X76.3008 Y13.2878 N130 G02 X71.5258 Y19.9946 I3.2005 J7.3319 N140 X71.7176 Y25.1168 I22.1421 J1.7355 N150 G03 X70.0732 Y54.0216 I-68.6576 J10.5932
58、N160 X61.301 Y68.2392 I-28.5532 J-7.8023 N170 X2.4997 Y-91.6959 I-61.301 J-68.2392 N180 X7.8237 Y-89.0099 I-.1908 J6.9974 第五章 參考文獻(xiàn) [1] 趙志修主編 《機械制造工藝削》 機械工業(yè)出版社 1985 [2] 袁哲俊主編 《金屬切削刀具》 上??茖W(xué)出版社 1993 [3] 李華主編 《機械制造技術(shù)》 北京工業(yè)出版社 1997 [4] 劉又午主編 《數(shù)字控制機床》 機械工業(yè)出版社
59、1983 [5] 李德慶主編 《機床數(shù)控技術(shù)》 機械工程師進(jìn)修大學(xué)出版 1987 [6] 駱志斌主編 《金屬工藝削》 高等教育出版社 1989 [7] Tooling and Production . 1962-1989 [8] Metalworking Production 1962-1965 小結(jié): 通過一個月的畢業(yè)設(shè)計,我們學(xué)到了很多知識,包括怎樣查閱資料,如何分析零件的結(jié)構(gòu)和安排工藝路線,如何選街刀具和機床夾具;每一到工序的進(jìn)給量和切削速度等,這些實用的知識,為我們以后的工作奠定了基礎(chǔ),使我們能夠盡快融入工作崗位上去。最重要的一點是經(jīng)過一個月的辛苦學(xué)習(xí),讓我們擺正了工作的態(tài)度,使以后能更好學(xué)習(xí)的前提。 致謝: 要說在這一個月中,有比我們還累的人,那就是我們的輔導(dǎo)老師了,曲云山老師不辭勞苦,百忙之中還要給我們來指導(dǎo),而且一星期來兩次,每次都要指導(dǎo)我們?nèi)⑺膫€小時,遇到有的學(xué)生沒思路,曲老師又會帶著他們找個工廠看實物,分析他們的結(jié)構(gòu),讓學(xué)生自己畫出裝配圖來加深理解。有時曲老師一天要跑好幾個地方,但是他依然無怨無悔,只求我們能做好設(shè)計,對此我們報以最衷心的感謝。 21
- 溫馨提示:
1: 本站所有資源如無特殊說明,都需要本地電腦安裝OFFICE2007和PDF閱讀器。圖紙軟件為CAD,CAXA,PROE,UG,SolidWorks等.壓縮文件請下載最新的WinRAR軟件解壓。
2: 本站的文檔不包含任何第三方提供的附件圖紙等,如果需要附件,請聯(lián)系上傳者。文件的所有權(quán)益歸上傳用戶所有。
3.本站RAR壓縮包中若帶圖紙,網(wǎng)頁內(nèi)容里面會有圖紙預(yù)覽,若沒有圖紙預(yù)覽就沒有圖紙。
4. 未經(jīng)權(quán)益所有人同意不得將文件中的內(nèi)容挪作商業(yè)或盈利用途。
5. 裝配圖網(wǎng)僅提供信息存儲空間,僅對用戶上傳內(nèi)容的表現(xiàn)方式做保護處理,對用戶上傳分享的文檔內(nèi)容本身不做任何修改或編輯,并不能對任何下載內(nèi)容負(fù)責(zé)。
6. 下載文件中如有侵權(quán)或不適當(dāng)內(nèi)容,請與我們聯(lián)系,我們立即糾正。
7. 本站不保證下載資源的準(zhǔn)確性、安全性和完整性, 同時也不承擔(dān)用戶因使用這些下載資源對自己和他人造成任何形式的傷害或損失。
最新文檔
- 設(shè)備采購常用的四種評標(biāo)方法
- 車間員工管理須知(應(yīng)知應(yīng)會)
- 某公司設(shè)備維護保養(yǎng)工作規(guī)程
- 某企業(yè)潔凈車間人員進(jìn)出管理規(guī)程
- 企業(yè)管理制度之5S管理的八個口訣
- 標(biāo)準(zhǔn)化班前會的探索及意義
- 某企業(yè)內(nèi)審員考試試題含答案
- 某公司環(huán)境保護考核管理制度
- 現(xiàn)場管理的定義
- 員工培訓(xùn)程序
- 管理制度之生產(chǎn)廠長的職責(zé)與工作標(biāo)準(zhǔn)
- 某公司各級專業(yè)人員環(huán)保職責(zé)
- 企業(yè)管理制度:5S推進(jìn)與改善工具
- XXX公司環(huán)境風(fēng)險排查及隱患整改制度
- 生產(chǎn)車間基層管理要點及建議