畢業(yè)設(shè)計(jì)論文 外文文獻(xiàn)翻譯 中英文對(duì)照 低透氣性煤層瓦斯突出卸壓原理及工程運(yùn)用
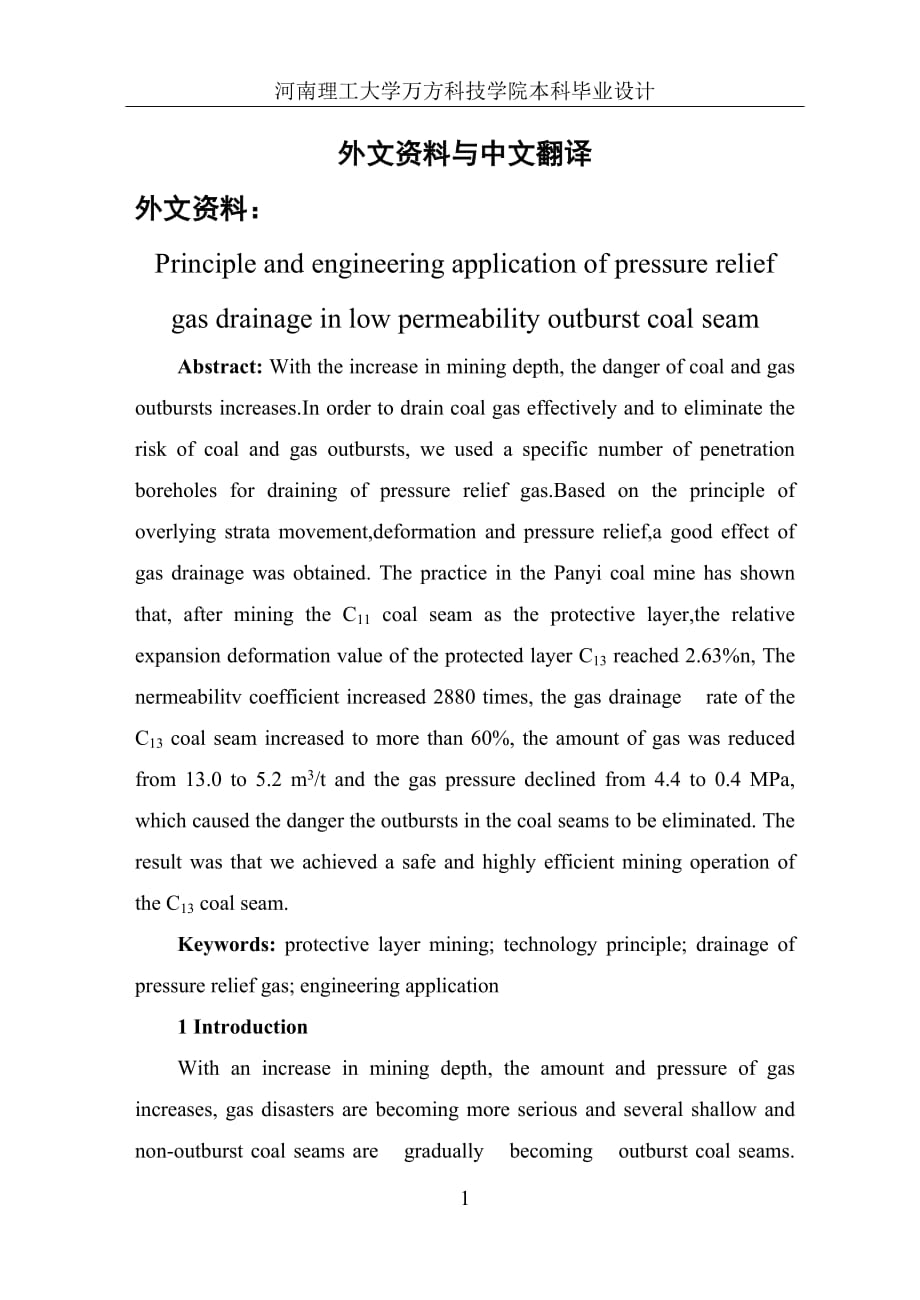


《畢業(yè)設(shè)計(jì)論文 外文文獻(xiàn)翻譯 中英文對(duì)照 低透氣性煤層瓦斯突出卸壓原理及工程運(yùn)用》由會(huì)員分享,可在線閱讀,更多相關(guān)《畢業(yè)設(shè)計(jì)論文 外文文獻(xiàn)翻譯 中英文對(duì)照 低透氣性煤層瓦斯突出卸壓原理及工程運(yùn)用(21頁(yè)珍藏版)》請(qǐng)?jiān)谘b配圖網(wǎng)上搜索。
1、河南理工大學(xué)萬(wàn)方科技學(xué)院本科畢業(yè)設(shè)計(jì) 外文資料與中文翻譯 外文資料: Principle and engineering application of pressure relief gas drainage in low permeability outburst coal seam Abstract: With the increase in mining depth, the danger of coal and gas outbursts increases.In order to drain coal gas effectively and to eliminate the
2、risk of coal and gas outbursts, we used a specific number of penetration boreholes for draining of pressure relief gas.Based on the principle of overlying strata movement,deformation and pressure relief,a good effect of gas drainage was obtained. The practice in the Panyi coal mine has shown that, a
3、fter mining the C11 coal seam as the protective layer,the relative expansion deformation value of the protected layer C13 reached 2.63%n, The nermeabilitv coefficient increased 2880 times, the gas drainage rate of the C13 coal seam increased to more than 60%, the amount of gas was reduced from 13.0
4、 to 5.2 m3/t and the gas pressure declined from 4.4 to 0.4 MPa, which caused the danger the outbursts in the coal seams to be eliminated. The result was that we achieved a safe and highly efficient mining operation of the C13 coal seam. Keywords: protective layer mining; technology principle; drain
5、age of pressure relief gas; engineering application 1 Introduction With an increase in mining depth, the amount and pressure of gas increases, gas disasters are becoming more serious and several shallow and non-outburst coal seams are gradually becoming outburst coal seams. Today, China has bec
6、ome the country with the most serious coal and gas outburst disasters in the entire world. Globally, our frequency and intensity of outbursts are the most severe. In contrast, coal and gas outbursts coal mines had been stopped production in the USA, Australia, Russia and other countries. According t
7、o a statistical analysis by expert consultants in 2005, among 415 coal mines of the 45 major monitored state owned coal enterprises, 234 mines are high gas and outburst coal mines, accounting for 56.4% of the major coal mines and 142 mines are subjected to coal and gas outbursts, accounting for 34.
8、2%. Usually, the permeability coefficient of outburst coal seams is low. For example, on average, this coefficient in the C13 coal seam of the Huainan ore area was only 0.011 m2/(MPa2.d), which presented great difficulties in pre-drainage of gas and in gas control to prevent outbursts in coal seams
9、. Based on the current condition of coal seams in the Panyi coal mine, we adopted a protective layer in our mining technology to drain pressure relief gas from protected seams,using RC net penetration boreholes in floor roadways, effectively reducing its gas content, completely eliminating the dan
10、ger of outbursts and achieved safe and highly efficient mining conditions. 2 General situation of test area The Panyi coal mine is a large mine designed for 3Mt production capacity. The C13 coal seam is one of its primary and most productive coal seams, which contained a large amount of gas und
11、er high pressure.A large number of outburst accidents have formerly occurred during mining, including a major gas explosion, so control over coal gas was very urgent before we could exploit this coal seam. The test area was located between the East-1 and East-2 mining areas, with the B 11 coal seam
12、 as a protective layer. We planned to combine mining the 21511 working face in East-1 and the 23521 in East-2 and called the combination 23521 instead The strike of the face is 1640 m and the trend 190 m.The thickness of the coal seam is between 1.5~2.4 m,2.0 m on average and the dip angle 60-130, 9
13、0 on average. The amount of gas of the B11 coal seam is 4-7.5m3/t and it is a non-outourst coat seam.The coal seam is stable and its geological structure simple.Fully mechanized coal mining technology had been adopted for the working face, designed for 2000 t/d. The C13 coal seam is a protected lay
14、er, located 70m above the B11 coal seam. The corresponding test working face of the protected layer consists of the 21213 working face in East-1 and the 23223 in East-2 (called 21213/23223 combined). The strike is 1680 m (two faces in all) and the trend is 160 m.The coal seam is 5.57~6.25 m thick, 6
15、.0 m on average,the dip angle 60~130 and 90 on average. The original measured gas pressure was 4.4 MPa, the amount of gas 13.0m3/t and the original permeability coefficient only 0.011 m2/(MPa2.d). The coal seam was also stable and its geological structure simple. By draining the pressure relief gas,
16、 the danger of outbursts in the C13 coal seam could be eliminated and the amount of gas was effectively reduced.A comprehensive,mechanized cover caving coal mining technology been adopted for this working face, which was signed for 5000 t/d. 3 Drainage principle of pressure relief gas Draining of
17、pressure relief gas is referred to as protective layer mining technology. When we mine coal seams in outburst coal mines, we should first mine the non-outburst or low risk outburst coal seams as protective layers, where the outburst coal seam is then called the protected layer. With protective layer
18、 mining, the coal and rock mass among the roof and floor moves and deforms within certain limits,which causes stress changing. Fracture fields are redistributed, ground stress is reduced, the coal seam expands, the coal seam permeability coefficient increases and drainage condition are created for p
19、ressure relief gas in the protected coal seams. In the case of the Panyi mine, we drilled penetration boreholes or carried out surface well drilling to drain the pressure relief gas, which caused the amount of gas and pressure to decrease significantly and the coal mass turned hard. Naturally. eas p
20、ressure reduced to below 0.5MPa, the amount of gas reauced to below a 6m3/t and the coal consistency coefficient rose 48%-100%.At the end, the danger of outbursts was completely eliminated from the protected layers and conditions for safe and highly efficient mining had been achieved. Drainage indic
21、es of pressure relief gas in the different ore areas are shown in Table 1. 4 Drainage methods of pressure relief gas Drainage methods of pressure relief gas consist largely of draining gas from the protected layers affected by mining. The space between the protective working faces 23521 and 212
22、13/23223 was about 70 m, which is really a long distance below the protective layer mining. We have often used surface well drilling and upper penetration boreholes located in floor roadways to drain pressure relief gas from the underside of the protective mining layer. Surface well drilling is unre
23、liable and we often used penetration boreholes. The design of penetration boreholes includes the construction of a floor roadway, a suction drilling field and upper penetration boreholesAll construction activities should be completed before starting mining the protective layer and we should ensure t
24、hat the pressure relief gas has been drained simultaneously with mining the protective layer. 4.1 Design and construction of the floor roadway Based on the occurrence of coal strata and concrete geologic conditions, the floor roadway was located 10-20 m below the C13 coal seam in a good lithology
25、rock bed and 4656 m from the protective layer.On the one hand, this position assured safe excavation, avoided gas inrush from the C13 coal seam and prevented the excavation of another coal seam by mistake. On the other hand, this location did not affect the mining of the B11 coal seam and assured no
26、rmal functions for gas draining. The floor roadway was located in the middle of the working face of the protected layer on the strike where,in principle,one should insist on avoiding forming down holes.The proportion of the section of the floor roadway was designed for 6 m2 4.2 Design and construct
27、ion of the suction drilling field At working face 23223, 51 fields had been constructed west forward and away from the stopping line in the floor roadway under the C13 coal seam. In the pressure relief area, a field was set every 40 m, so the pressure relief area of face 21213/23223 in the protecte
28、d layer needed 39 fields in all. According to the pressure relief angle, non pressure relief areas were present in the protected layer, with a field every 10 m, so that the non pressure relief areas of face 23223 in the protected layer needed only three fields and nine in face 21213. The drilling f
29、ield was perpendicular to the floor roadway,with a length of 5m and a net section proportion of 6.16 m2 Bolt-shotcrete support technology had been adopted. 4.3 Design and construction of upper penetration boreholes Every drilling field had 4 holes set on the strike in the pressure relief area. The
30、 space between holes was 40 m, which was oriented on the middle of the thick-surface of the coal seam. The position of the hole opening was located at the top of the drilling field and the final hole position ended 0.5 m into the roof of the C13 coal seam. Its design is shown in Fig.1. The total len
31、gth of the draining holes was 8879 m,of which 1460 m was drilled through the C13 coal seam. The space between holes was 10 m in the non pressure relief area. 5 Pressure relief level After mining the protective layer, this layer moved and deformed, which caused ground stress to reduce,the perme
32、ability coefficient to increase and pressure relief occurred. Pressure relief levels are related to the space of the layer, rock lithology, mining height and so on. The levels are higher and the pressure relief effect is better in the protected layer. The change of ground stress can visibly reflect
33、the pressure relief level, but the stress is hard to measure in the field, so we adopted the extent of coal deformation and the coal seam permeability coefficient to reflect the level indirectly. 5.1 Relative deformation We adopted a base point method to investigate the deformation of the C13 coal
34、 seam. To start, we drilled a deep hole, and then installed test points in the roof and floor of the C13 coal seam, where the deformation was determined by the relative displacement of the two test points. The measured results are shown in Fig.2. We can see that, during mining of the B11 coal seam,
35、the C13 coal seam was first compressed, and then expanded, the maximum compression deformation was 27 mm and the maximum expansion deformation 210.44 mm, so that the maximum relative compression deformation was 0.337%, and the maximum relative expanding deformation 2.63%. The bigger the expansion de
36、formation, the better the effect of pressure relief. 5.2 Variation of permeability coefficient The orieinal coal seam nermeabilitv coefficient was only 0.011m2/(MPa2.d).After mining the B11 coal seam, the pressure was relieved from the C13 coal seam and the permeability coefficient clearly incre
37、ased. By using the amounts of residual gas and the borehole gas inrush, we calculated that the permeability coefficient had increased to 32.687 m2(MPa2.d), an increase of almost 2880 times, which indicated that the C13 coal seam was now in the condition where gas has been drained. 6 Drainage effect
38、 of pressure relief gas 6.1 Amount and rate of gas drainage 1) Analysis of drainage of pressure relief gas When the protective working face advanced 40 m over the suction drilling field, the amount of gas drained rapidly increased. Fig.3 shows the variation in the amount of gas drainage vs.time i
39、n the drilling yard of the Huainan coal mine. The original 20 days was the period of increased gas drainage, enhanced pressure releasing activity and the amount of gas drainage increased. The period between 20-80 days was the active period of gas drainage, the pressure release activity became regula
40、r and permeability reached a maximum. Gas drainage was regular and the amount of gas drained from a single hole was over 1.0 m3/min. After day 80 the attenuation period set in, where the coal seam became gradually compacted, permeability reduced, the residual pressure became small and the amount of
41、 gas drainage reduced exponentially. According to this research, a highly effective drainage period was 2 months, the length of the affected area was 160 m and the number of active drainage holes was 16. On average, the amount of gas drained from a single hole was about 1.0 m3/min Aftter 4 months of
42、 continuous gas drainage ,the rate of gas drainage reached over 60%. 2) Total amount of gas drainage and amount of residual gas The total amount of gas drainage includes the amount drained from penetration boreholes and wind emission in the floor roadway. The period of working face 21213 for whi
43、ch statistics were obtained was from Feb.1, 2000 to Jan. 31, 2001, 365 days in all.The accumulated amount of gas drainage by penetralion boreholes was 7.99Mm3 and the amount by wind emission 0.74 Mm3. The reserves of the protected layer were 14.68 Mm3 and the total amount of gas drainage 8.73Mm3,so
44、 that the rate of gas drainage reached 60%. The amount of gas inrush and amount of gas flowing into work-out areas of the protective layer were not inccluded in our calculation, so that the actual rate of gas drainage was larger than the calculated value,i.e.,a rate over 60%. Since the orieinal amou
45、nt of eas of the C13 coal seam was 13m3/t. the restauai eas content was 5.2m3/t, given our calculations. 6.2 Gas pressure With the advancement of the working face, the pressure gauge value gradually decreased from 4.4MPa, when the working face was 100 m away from the pressure measured hole; when
46、80 m away, the pressure sharply decreased, and at 62 m the pressure gauge finger pointed to zero. When the protective working face advanced 400m past the pressure measured hole, the pressure value increased from zero to 0.4 MPa and remained stable, which indicated that the residual gas pressure was
47、0.4MPa. 6.3 Outburst danger eliminated analysis of the protected layer The amount of gas in the protected layer is decreased by draining the pressure relief gas.The amount of residual as of the C13 coal seam was reduced to 5.2 and the residual declined to 0.4 MPa. The amount of gas pressure values
48、 were lower than the critical value, which was 8m3/t for the amount gas and 0.74MPa (pressure gauge) for gas pressure.All this shows is that C13 coal seam had changed from a high gas and outburst coal seam to a low non-outburst coal and C13 became a safe and highly effective coal seam where mining
49、 conditions became considerably better, as proven by its current mining practice. 7 Conclusions 1) With the advancement of a working face, coal and rock masses among the roof and floor move and become deformed within certain limits, ground stress is reduced, coal seams expand and the coal seam per
50、meability coefficient increases in outburst coal seams. After mining of the Bllcoal seam, the maximum relative compression deformation of the C13 coal seam was 0.337% and the maximum relative expansion deformation 2.63%. The permeability coefficient increased almost 2880 times and favourable conditi
51、ons for drainage of pressure relief gas were obtained in the protected coal seam C13. 2) The most effective gas drainage method is the use of upper RC net penetration boreholes in the floor roadway. For an optimum pressure relief level, the space between holes should be 40 m in the pressure relief
52、area and 10m in the non pressure relief area. 3) After gas draining of the C13 coal seam,the amount of gas in the C13 coal seam effectively decreased,from 13.0m3/t to 5.2m3/t and the rate of gas drainage reached above 60%. The gas pressure was reduced from 4.4MPa to 0.4MPa. In the end, the danger o
53、f outbursts had been completely eliminated in the protected layer and safe and highly efficient mining conditions had been achieved. Acknowledgements The authors are grateful to the National Basic Research Program of China, and the National Natural Science Foundation of China for their support Sci
54、ence Foundation of China for their support. [1] Cheng Y P, Yu Q X. Developmet of regional gas control technology for Chinese coalmines. Journal of Mining and Safety Engineering, 2007, 24(4): 383-390. (In Chinese). [2] Cheng Y P, Yu Q X. Application of safe and high-efficient exploitation system of
55、 coal and gas in coal seams.Journal of China University of Mining & Technology,2003, 32(5): 471-475. (In Chinese). [3] Wang H F, Cheng Y P, Yu Q X, Zhou Z Y, Zhou H X,Liu H Y Research on the amount of safe mineable coal in mines susceptible to coal and gas outburst Journal of China University of Mi
56、ning & Technology, 2008, 37(2):236-240. (In Chinese). [4] Cheng Y P, Yu Q X, Yuan L, Li P, Liu Y Q, Tong Y F.Experimental research of safe and high-efficient exploitation of coal and pressure relief gas in long distance.Journal of China University of Mining & Technology,2004, 33(2): 132-136. (In Ch
57、inese). [5] State Administration of Coal Mine Safety. Coal Mine Safety Regulation. Beijing: China Coal Industry Publishing House, 2007: 113-119. [6] Yu Q X. The Prevention and Control of Gas in Coal Mines. Xuzhou: China University of Mining and Technology Press, 1992. (In Chinese) [7] Liu L. Reli
58、ef gas drainage technology during distant under-protect seam reining. Mining Safety & Environmental Protection, 2007, 34(6): 45-47. (In Chinese). [8] Wang L, Cheng Y P, Li F R, Wang H F, Liu H B. Fracture evolution and pressure relief gas drainage from distant protected coal seams under an extremel
59、y thick key stratum. Journal of China University of Mining & Technology, 2008, 18(2): 182-186. [9] State Administration of Coal Mine Safety. Gas Drainage Basic Index in Coal Mine (AQ 1026-2006), 2006. (In Chinese) 中文翻譯: 低透氣性煤層瓦斯突出卸壓原理及工程運(yùn)用 摘要:隨著開(kāi)采深度的增加,瓦斯突出危險(xiǎn)也隨之增加。為了能夠有效地釋放瓦斯壓力,消除瓦斯突出的風(fēng)險(xiǎn),我們
60、使用一個(gè)特定數(shù)量的滲透鉆孔抽瓦斯。由于過(guò)度的巖層運(yùn)動(dòng),變形減壓原則獲得一個(gè)好的氣體引流效果。潘一礦實(shí)踐表明,作為保護(hù)層開(kāi)采的C1l煤層,被保護(hù)層的相對(duì)擴(kuò)張變形值C13達(dá)到2.63%!滲透系數(shù)增加了2880倍,C13煤層瓦斯抽放率增加到60%以上,氣體量從13.0m3/t降低到5.2m3/t,氣體壓力從4.4MPa下降到0.4MPa,這使得在煤礦中造成突出的危險(xiǎn)消除。這就使我們?cè)贑13煤層實(shí)現(xiàn)了一個(gè)安全、高效的采煤作業(yè)環(huán)境。 關(guān)鍵詞:保護(hù)層 技術(shù)原理 引流減壓瓦斯 工程應(yīng)用 1引言 隨著開(kāi)采深度的增加,瓦斯的含量量和壓力增加,瓦斯災(zāi)難變得更加嚴(yán)重些,一些淺和不爆發(fā)的煤層也逐漸變成突
61、出煤層?,F(xiàn)在,中國(guó)已成為全世界煤與瓦斯突出災(zāi)害最嚴(yán)重的國(guó)家,在全球范圍內(nèi),我們國(guó)家瓦斯突出的強(qiáng)度是最嚴(yán)重的。相比之下,在美國(guó)、澳洲、俄羅斯、和其他國(guó)家煤和瓦斯爆炸已經(jīng)不再出現(xiàn)了。根據(jù)2005年專(zhuān)家顧問(wèn)的統(tǒng)計(jì)分析數(shù)據(jù),在415個(gè)煤礦中有45個(gè)重大的國(guó)有控制煤礦企業(yè),234個(gè)高瓦斯礦,占主要煤礦的56.4%,142個(gè)煤礦有瓦斯突出,占34.2%。 通常,煤層的低滲透系數(shù)低,例如,平均來(lái)說(shuō),在淮南地區(qū)的開(kāi)采的煤層中C13的系數(shù)只有0.01~1m2/(MPa2.d),它目前最大的困難在提前排出瓦斯控制在煤層中發(fā)生瓦斯突出?;诋?dāng)前潘一煤礦的煤層狀況,在開(kāi)采中我們采用了開(kāi)采保護(hù)層開(kāi)采技術(shù)進(jìn)而從保護(hù)層釋
62、放瓦斯,在底板使用鋼筋混泥土網(wǎng)狀滲透鉆孔,有效地降低其瓦斯的含量,完全消除突出的危險(xiǎn),取得了安全、高效的開(kāi)采環(huán)境。 2 測(cè)試區(qū)概況 潘一煤礦是一個(gè)有3Mt生產(chǎn)能力的的大型煤礦。C13煤層是它主要開(kāi)采煤層,它包含著高壓下大量的天然氣。大量的突出事故發(fā)生在開(kāi)采中,包括一個(gè)重大瓦斯爆炸事故,所以在開(kāi)采這個(gè)煤層之前,控制瓦斯含量非常重要。 測(cè)試區(qū)位于東1和東2礦區(qū),B11煤層作為保護(hù)層。我們計(jì)劃結(jié)合開(kāi)采工作面東1礦區(qū)21511和在東2礦區(qū)23521。開(kāi)采的的煤層深度是190m到1600m,煤層厚度是平均1.5米~2.4米,傾角平均6~13。B11煤層是4~7.5m/t,它是非突出煤層,由于煤層
63、穩(wěn)定且其地質(zhì)結(jié)構(gòu)簡(jiǎn)單,采用綜采日產(chǎn)量2000t。 C13煤層是一個(gè)保護(hù)層,在B11煤層之上間距70米。相應(yīng)測(cè)試開(kāi)采層的保護(hù)護(hù)層由東1礦區(qū)的21213工作面和東2礦區(qū)(21213工作面/23223工作面的總和)構(gòu)成,開(kāi)采煤層是深度從160m到1600m包含兩層煤。煤層平均有5.57~6.25 m厚,傾角平均6~9。原始瓦斯壓力是4.4MPa,瓦斯含量是13.0m/ t,原始煤層滲透系數(shù)僅為0.01~l㎡/(MPa.d)煤層也穩(wěn)定且其地質(zhì)結(jié)構(gòu)簡(jiǎn)單。通過(guò)釋放瓦斯壓力,在C13煤層突出的危險(xiǎn)可以被消除并且瓦斯的數(shù)量可以有效地減少,采用綜采日產(chǎn)量5000t。 3 瓦斯壓力原則 瓦斯壓力釋放被作為一
64、種被保護(hù)層開(kāi)采技術(shù)。當(dāng)我們?cè)谝装l(fā)生瓦斯爆炸的煤礦開(kāi)采時(shí),我們首先把不發(fā)生突出或著低煤層突出危險(xiǎn)的煤層作為保護(hù)層,那些突出煤層的地方被稱(chēng)為被保護(hù)層。隨著保護(hù)層的開(kāi)采,頂部和底部的煤層和巖石層移動(dòng)并在一定范圍內(nèi)變形,這導(dǎo)致壓力改變。易碎層重新分配,地面壓力減小,煤層擴(kuò)大,煤層透氣性系數(shù)增加,從而使在保護(hù)層排泄條件有利于緩解瓦斯壓力。在潘一煤礦的例子中,我們用鉆孔或進(jìn)行透氣鉆孔引流減少瓦斯壓力和含量,這造成的瓦斯含量和壓力顯著降低并使煤炭質(zhì)量變硬。當(dāng)然,瓦斯壓力減少到低于0.5MPa.,氣體量減少到低于6m/t,煤炭的濃度系上漲48%~100%。最終,突出的危險(xiǎn)完全被排除在被保護(hù)層,安全高效率的開(kāi)采
65、條件得以實(shí)現(xiàn)。在不同巖層排放瓦斯的指數(shù)領(lǐng)域如表1所示 地名 層空間(m) 相對(duì)擴(kuò)大變形 透氣系數(shù)增加的倍數(shù) 抽放率 瓦斯含量 瓦斯壓力 采煤點(diǎn) 淮南潘一礦 70 2.63 2880 60.0 5.2 0.4 下保護(hù)層 沈陽(yáng)紅領(lǐng)礦 16 0.72 1010 77.5 5.06 0.35 上保護(hù)層 淮南謝一礦 19 0.4 68.0 4.3 0.5 上保護(hù)層 陽(yáng)泉三礦 125 0.784 68.8 5.76 下保護(hù)層 4瓦斯壓力的排放途徑 瓦斯壓力的排放途徑包含在開(kāi)采過(guò)程中大量從保護(hù)層釋放出來(lái)的瓦斯。保護(hù)
66、層開(kāi)采的是23521工作面和21213/23223工作面間距有70m,這是低于保護(hù)層開(kāi)采的距離。我們經(jīng)常使用的地表打鉆和巷道鉆孔,通過(guò)鉆孔排出瓦斯使保護(hù)層的下部卸壓。地面打鉆是不可靠的,我們經(jīng)常使用的穿層鉆孔,穿層鉆孔的設(shè)計(jì)包括巖層大巷的建設(shè),鉆場(chǎng)和穿層鉆孔。所有準(zhǔn)備工作應(yīng)在開(kāi)采被保護(hù)層之前完成,隨之開(kāi)采被保護(hù)層時(shí),我們應(yīng)該確保瓦斯含量已經(jīng)排到臨界值以下。 4.1巷道的設(shè)計(jì)與施工 基于煤層條件和具體的地質(zhì)條件,巷道在C13煤層以下10~20米較好的巖層里布置或在C13煤層以上46~56米較好的巖層。一方面,這個(gè)位置要保證安全,避免氣體從C13煤層涌出,防止另一個(gè)煤層開(kāi)挖的錯(cuò)誤。另一方面,這個(gè)位置并不影響B(tài)11煤層的開(kāi)采保證正常的瓦斯抽放的。巖層巷道沿走向位于作業(yè)場(chǎng)所的中間保護(hù)層,原則上,我們應(yīng)該堅(jiān)持避免形成地下洞,巷道的斷面是6m2。 4.2鉆場(chǎng)抽放的設(shè)計(jì)與構(gòu)建 在23223工作面,51鉆場(chǎng)已經(jīng)建成,遠(yuǎn)離C13煤層巷道禁止線,在減壓區(qū),每一個(gè)區(qū)段的設(shè)置是40m。所以減壓區(qū)的表面為21213/23223在防護(hù)層總共需要39個(gè)鉆場(chǎng)。根據(jù)減壓角度、非減壓區(qū)目前在被保
- 溫馨提示:
1: 本站所有資源如無(wú)特殊說(shuō)明,都需要本地電腦安裝OFFICE2007和PDF閱讀器。圖紙軟件為CAD,CAXA,PROE,UG,SolidWorks等.壓縮文件請(qǐng)下載最新的WinRAR軟件解壓。
2: 本站的文檔不包含任何第三方提供的附件圖紙等,如果需要附件,請(qǐng)聯(lián)系上傳者。文件的所有權(quán)益歸上傳用戶(hù)所有。
3.本站RAR壓縮包中若帶圖紙,網(wǎng)頁(yè)內(nèi)容里面會(huì)有圖紙預(yù)覽,若沒(méi)有圖紙預(yù)覽就沒(méi)有圖紙。
4. 未經(jīng)權(quán)益所有人同意不得將文件中的內(nèi)容挪作商業(yè)或盈利用途。
5. 裝配圖網(wǎng)僅提供信息存儲(chǔ)空間,僅對(duì)用戶(hù)上傳內(nèi)容的表現(xiàn)方式做保護(hù)處理,對(duì)用戶(hù)上傳分享的文檔內(nèi)容本身不做任何修改或編輯,并不能對(duì)任何下載內(nèi)容負(fù)責(zé)。
6. 下載文件中如有侵權(quán)或不適當(dāng)內(nèi)容,請(qǐng)與我們聯(lián)系,我們立即糾正。
7. 本站不保證下載資源的準(zhǔn)確性、安全性和完整性, 同時(shí)也不承擔(dān)用戶(hù)因使用這些下載資源對(duì)自己和他人造成任何形式的傷害或損失。
最新文檔
- 2023年六年級(jí)數(shù)學(xué)下冊(cè)6整理和復(fù)習(xí)2圖形與幾何第7課時(shí)圖形的位置練習(xí)課件新人教版
- 2023年六年級(jí)數(shù)學(xué)下冊(cè)6整理和復(fù)習(xí)2圖形與幾何第1課時(shí)圖形的認(rèn)識(shí)與測(cè)量1平面圖形的認(rèn)識(shí)練習(xí)課件新人教版
- 2023年六年級(jí)數(shù)學(xué)下冊(cè)6整理和復(fù)習(xí)1數(shù)與代數(shù)第10課時(shí)比和比例2作業(yè)課件新人教版
- 2023年六年級(jí)數(shù)學(xué)下冊(cè)4比例1比例的意義和基本性質(zhì)第3課時(shí)解比例練習(xí)課件新人教版
- 2023年六年級(jí)數(shù)學(xué)下冊(cè)3圓柱與圓錐1圓柱第7課時(shí)圓柱的體積3作業(yè)課件新人教版
- 2023年六年級(jí)數(shù)學(xué)下冊(cè)3圓柱與圓錐1圓柱第1節(jié)圓柱的認(rèn)識(shí)作業(yè)課件新人教版
- 2023年六年級(jí)數(shù)學(xué)下冊(cè)2百分?jǐn)?shù)(二)第1節(jié)折扣和成數(shù)作業(yè)課件新人教版
- 2023年六年級(jí)數(shù)學(xué)下冊(cè)1負(fù)數(shù)第1課時(shí)負(fù)數(shù)的初步認(rèn)識(shí)作業(yè)課件新人教版
- 2023年六年級(jí)數(shù)學(xué)上冊(cè)期末復(fù)習(xí)考前模擬期末模擬訓(xùn)練二作業(yè)課件蘇教版
- 2023年六年級(jí)數(shù)學(xué)上冊(cè)期末豐收?qǐng)@作業(yè)課件蘇教版
- 2023年六年級(jí)數(shù)學(xué)上冊(cè)易錯(cuò)清單十二課件新人教版
- 標(biāo)準(zhǔn)工時(shí)講義
- 2021年一年級(jí)語(yǔ)文上冊(cè)第六單元知識(shí)要點(diǎn)習(xí)題課件新人教版
- 2022春一年級(jí)語(yǔ)文下冊(cè)課文5識(shí)字測(cè)評(píng)習(xí)題課件新人教版
- 2023年六年級(jí)數(shù)學(xué)下冊(cè)6整理和復(fù)習(xí)4數(shù)學(xué)思考第1課時(shí)數(shù)學(xué)思考1練習(xí)課件新人教版
相關(guān)資源
更多